Ciencia al descubierto
Ciencia al descubierto
Modernización de sistemas de control
para unidades generadoras del tipo turbogás
para unidades generadoras del tipo turbogás
Modernización de sistemas de control
para unidades generadoras del tipo turbogás
para unidades generadoras del tipo turbogás
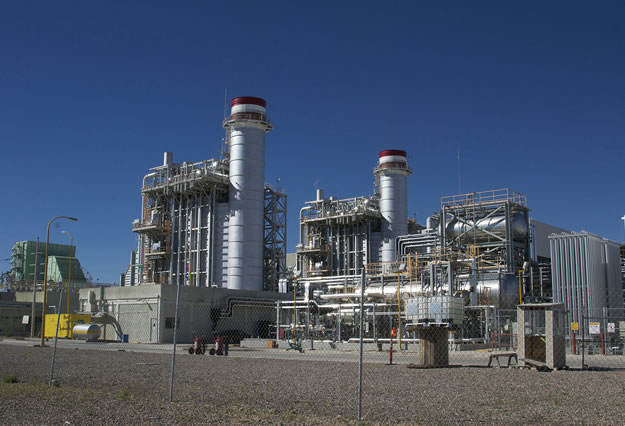
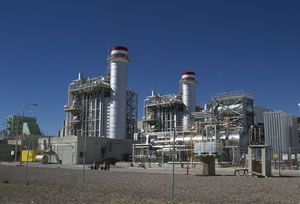
Resumen
Resumen
En este artículo se analiza la necesidad de modernizar los
sistemas de control de los equipos principales de las centrales
generadoras, con el fin de incrementar su confiabilidad
en la operación. Particularmente se describen los elementos
que justifican la modernización y cómo se relacionan con
los beneficios que podrían obtenerse. También se plantean
algunas de las justificaciones típicas que se pueden proponer
para determinar si tales modificaciones son apropiadas, así
como los alcances considerados en la modernización.
Introducción
Introducción
La generación de energía eléctrica en México actualmente
es muy diversa por su tecnología, comprende desde vapor
(combustóleo o gas), carboeléctrica, geotermoeléctrica, ciclo
combinado, turbogás, combustión interna, hidroeléctrica,
eoloeléctrica, hasta nucleoeléctrica y solar fotovoltaica. De
acuerdo con las necesidades del sistema eléctrico (demanda),
el cual suministra energía a los hogares e industrias, es el
tipo de tecnología que se utiliza para generar electricidad.
En los últimos años, más del 78% de la generación de energía eléctrica provino de tecnologías convencionales basadas en el uso de combustibles fósiles como energético primario. Estas tecnologías incluyen: carboeléctrica, ciclo combinado, combustión interna, termoeléctrica convencional y turbogás, principalmente.
De acuerdo con datos reportados por el PRODESEN 2018- 2032, el número de centrales eléctricas instaladas en México por tipo de tecnología es como lo muestra la tabla 1.
Tabla 1. Número de centrales eléctricas por tecnología. Fuente:PRODESEN 2018-2032.
En los últimos años, más del 78% de la generación de energía eléctrica provino de tecnologías convencionales basadas en el uso de combustibles fósiles como energético primario. Estas tecnologías incluyen: carboeléctrica, ciclo combinado, combustión interna, termoeléctrica convencional y turbogás, principalmente.
De acuerdo con datos reportados por el PRODESEN 2018- 2032, el número de centrales eléctricas instaladas en México por tipo de tecnología es como lo muestra la tabla 1.
Tecnología | Número de Centrales Eléctricas |
Ciclo Combinado | 83 |
Termoeléctrica Convencional | 59 |
Carboeléctrica | 3 |
Turbogás | 131 |
Combustión Interna | 248 |
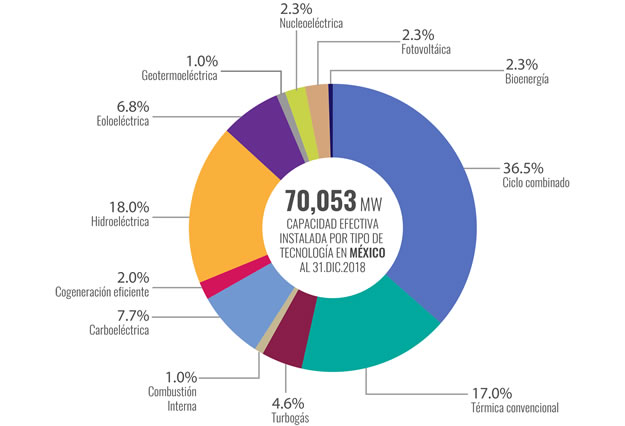
Figura 1. Capacidad efectiva instalada por tipo de tecnología, al 31 de diciembre de 2018.
Térmica convencional incluye lecho fluidizado (70,053 MW).
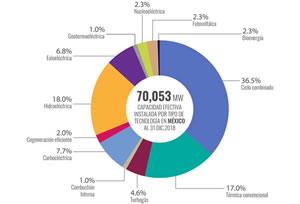
Figura 1. Capacidad efectiva instalada por tipo de tecnología, al 31 de diciembre de 2018.
Térmica convencional incluye lecho fluidizado (70,053 MW).
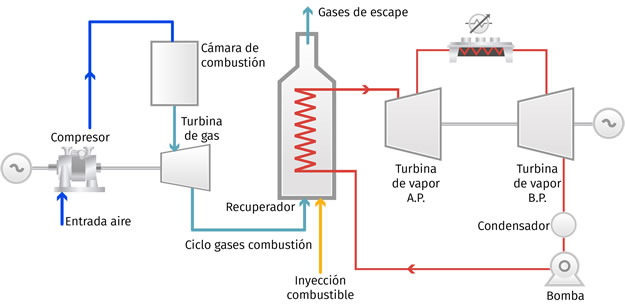
Figura 2. Diagrama simplificado de una central de ciclo combinado.
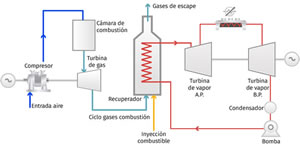
Figura 2. Diagrama simplificado de una central de ciclo combinado.
Central turbogás
Central turbogás
Una central turbogás está compuesta básicamente de un
dispositivo de arranque, un compresor, una cámara de
combustión, una turbina de gas, un generador eléctrico y
los sistemas auxiliares tales como el sistema de combustible,
el de lubricación, el de arranque, entre otros, como se
muestra en la figura 3.
El dispositivo de arranque es un equipo cuyo objetivo es asistir a la unidad de generación durante la fase de arranque, para vencer la inercia y acelerar la turbina de gas hasta la velocidad de inicio de la combustión (ignición). El compresor centrífugo presuriza el aire de la atmósfera y lo envía a la cámara de combustión, en donde se realiza la combustión del combustible gas o diésel. Los gases de escape de alta presión, producto de la combustión, se expanden en las etapas de la turbina para hacer girar a la unidad. El generador eléctrico acoplado a la turbina de gas, a velocidad nominal, es capaz de generar energía eléctrica. Finalmente, los gases de escape se descargan a la atmósfera.
Existen dos tipos principales de turbina de gas: industrial o aeroderivada; en función a su capacidad, relación de compresión, flujo de aire y temperaturas de operación, las cuales tienen respuestas y desempeños diferentes ante modificaciones de las condiciones atmosféricas.
Turbinas de gas aeroderivadas: provienen del diseño de turbinas para fines aeronáuticos, pero adaptadas a la producción de energía eléctrica en plantas industriales o microturbinas.
Turbinas de gas industriales: diseñadas para la producción de electricidad, mejorando la eficiencia para obtener una mayor cantidad de potencia y largos periodos de operación a carga máxima, disminuyendo el número de paros y arranques continuos.
Las centrales tipo turbogás tienen la ventaja de entrar en funcionamiento en poco tiempo, permitiendo abastecer rápidamente la demanda de carga eléctrica en horas de mayor demanda (hora pico). Estas pueden operar en forma de fuente de energía auxiliar o en forma permanente.
El dispositivo de arranque es un equipo cuyo objetivo es asistir a la unidad de generación durante la fase de arranque, para vencer la inercia y acelerar la turbina de gas hasta la velocidad de inicio de la combustión (ignición). El compresor centrífugo presuriza el aire de la atmósfera y lo envía a la cámara de combustión, en donde se realiza la combustión del combustible gas o diésel. Los gases de escape de alta presión, producto de la combustión, se expanden en las etapas de la turbina para hacer girar a la unidad. El generador eléctrico acoplado a la turbina de gas, a velocidad nominal, es capaz de generar energía eléctrica. Finalmente, los gases de escape se descargan a la atmósfera.
Existen dos tipos principales de turbina de gas: industrial o aeroderivada; en función a su capacidad, relación de compresión, flujo de aire y temperaturas de operación, las cuales tienen respuestas y desempeños diferentes ante modificaciones de las condiciones atmosféricas.
Turbinas de gas aeroderivadas: provienen del diseño de turbinas para fines aeronáuticos, pero adaptadas a la producción de energía eléctrica en plantas industriales o microturbinas.
Turbinas de gas industriales: diseñadas para la producción de electricidad, mejorando la eficiencia para obtener una mayor cantidad de potencia y largos periodos de operación a carga máxima, disminuyendo el número de paros y arranques continuos.
Las centrales tipo turbogás tienen la ventaja de entrar en funcionamiento en poco tiempo, permitiendo abastecer rápidamente la demanda de carga eléctrica en horas de mayor demanda (hora pico). Estas pueden operar en forma de fuente de energía auxiliar o en forma permanente.
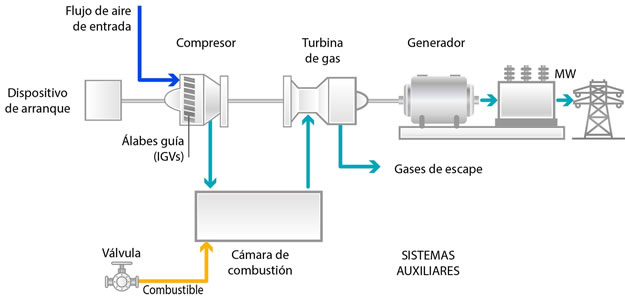
Figura 3. Diagrama simplificado de una unidad turbogás.

Figura 3. Diagrama simplificado de una unidad turbogás.
Sistema de control
Sistema de control
La unidad turbogás requiere de un sistema de control
que permita conducirla a través de las diferentes etapas
de operación, para lograr su fin que es la generación de
energía eléctrica. Estas etapas se pueden resumir de la
manera siguiente:
Arranque de la unidad desde velocidad cero hasta la velocidad de operación, que puede variar dependiendo del modelo de turbina ? generador.
Sincronización, que consiste en el proceso de conexión de la unidad turbogás a la red de distribución de energía eléctrica para aportar energía al sistema.
Generación de energía eléctrica de acuerdo con los valores establecidos por el fabricante.
Las funciones que realiza el sistema de control son básicamente las de regulación de las variables principales (velocidad, temperatura, potencia eléctrica, entre otras), supervisión y protección de la unidad generadora, incluyendo respuesta rápida, precisión y disponibilidad.
Los sistemas de control originales de las unidades turbogás de muchas centrales de la CFE se han degradado funcionalmente, ya que cuentan con más de 40 años de servicio y no existen partes de repuesto en el mercado, lo que hace que su mantenimiento sea cada vez más difícil y se presenten fallas en los arranques de las mismas. Además, existe el riesgo latente de incremento de salidas forzadas y fallas catastróficas en el equipo principal.
Si bien el equipo mecánico puede durar muchos años, el equipo de control e instrumentación tiene una vida útil limitada antes de que la obsolescencia del software o los componentes pueda dificultar cada vez más el mantenimiento, así como el del equipo instalado.
Dicha obsolescencia puede ser más importante para las empresas basadas en tecnología, donde la tecnología crítica utilizada es parte de su servicio o producción. También puede significar que ya no pueden ser competitivos dentro del mercado.
Así mismo, cabe resaltar el papel que juegan estas unidades para proporcionar energía eléctrica de emergencia en situaciones de demanda alta y/o eventos de falla de unidades de carga base, y su capacidad de arranque negro para restablecimiento expedito en el caso de un colapso del Sistema Eléctrico Nacional.
En el Instituto Nacional de Electricidad y Energías Limpias (INEEL) se han diseñado, construido, instalado y puesto en servicio, sistemas de control para turbinas de gas de diversos modelos, tal como se presenta en la tabla 2.
En estas modernizaciones se han utilizado equipos de tecnología reciente, con programación basada en estándares que permiten un mejor mantenimiento, así como ser reemplazados con mayor facilidad en un futuro, como son los Controladores Lógicos Programables (PLC, por sus siglas en inglés). Además de que es factible incluir el control digital de arranque/paro y la lógica de protecciones en el mismo equipo, con la consecuente disminución en costos.
Arranque de la unidad desde velocidad cero hasta la velocidad de operación, que puede variar dependiendo del modelo de turbina ? generador.
Sincronización, que consiste en el proceso de conexión de la unidad turbogás a la red de distribución de energía eléctrica para aportar energía al sistema.
Generación de energía eléctrica de acuerdo con los valores establecidos por el fabricante.
Las funciones que realiza el sistema de control son básicamente las de regulación de las variables principales (velocidad, temperatura, potencia eléctrica, entre otras), supervisión y protección de la unidad generadora, incluyendo respuesta rápida, precisión y disponibilidad.
Los sistemas de control originales de las unidades turbogás de muchas centrales de la CFE se han degradado funcionalmente, ya que cuentan con más de 40 años de servicio y no existen partes de repuesto en el mercado, lo que hace que su mantenimiento sea cada vez más difícil y se presenten fallas en los arranques de las mismas. Además, existe el riesgo latente de incremento de salidas forzadas y fallas catastróficas en el equipo principal.
Si bien el equipo mecánico puede durar muchos años, el equipo de control e instrumentación tiene una vida útil limitada antes de que la obsolescencia del software o los componentes pueda dificultar cada vez más el mantenimiento, así como el del equipo instalado.
Dicha obsolescencia puede ser más importante para las empresas basadas en tecnología, donde la tecnología crítica utilizada es parte de su servicio o producción. También puede significar que ya no pueden ser competitivos dentro del mercado.
Así mismo, cabe resaltar el papel que juegan estas unidades para proporcionar energía eléctrica de emergencia en situaciones de demanda alta y/o eventos de falla de unidades de carga base, y su capacidad de arranque negro para restablecimiento expedito en el caso de un colapso del Sistema Eléctrico Nacional.
En el Instituto Nacional de Electricidad y Energías Limpias (INEEL) se han diseñado, construido, instalado y puesto en servicio, sistemas de control para turbinas de gas de diversos modelos, tal como se presenta en la tabla 2.
En estas modernizaciones se han utilizado equipos de tecnología reciente, con programación basada en estándares que permiten un mejor mantenimiento, así como ser reemplazados con mayor facilidad en un futuro, como son los Controladores Lógicos Programables (PLC, por sus siglas en inglés). Además de que es factible incluir el control digital de arranque/paro y la lógica de protecciones en el mismo equipo, con la consecuente disminución en costos.
Justificación de la modernización
Justificación de la modernización
La modernización de los sistemas de control de las unidades
de generación, así como la actualización de las
Interfaces Hombre Máquina (IHM), tiene como fin principal
el mejorar la disponibilidad de las unidades y reducir los
costos de mantenimiento futuro.
Los elementos clave que justifican una modernización son:
Seguridad. Disminuir riesgo al personal, cumplir con la normatividad vigente, reactivación de turbinas en paro prolongado.
Disponibilidad. Sistema de control más confiable con tecnología nueva, redundancia en los controladores.
Confiabilidad. Operar de acuerdo con lo diseñado, mejor tecnología, mejor control.
Obsolescencia económica. Los controles mecánicos/ hidráulicos requieren márgenes de seguridad mayores que el control digital, son menos eficientes.
Mortandad del sistema de control. La vida útil promedio de los sistemas de control es de 15-20 años.
Obsolescencia técnica. Ante el desarrollo tecnológico, es posible adaptar funciones nuevas y lograr una mejor respuesta de los equipos principales.
Cambios operativos flexibles. En ocasiones, ante las exigencias del sistema eléctrico, es necesario modificar la generación de la unidad (carga base, cycling, peaking duty).
Tabla 2. Unidades Turbogás modernizadas por el INEEL.
CTG - Central Turbogás CT - Central Termoeléctrica
Los elementos clave que justifican una modernización son:
Seguridad. Disminuir riesgo al personal, cumplir con la normatividad vigente, reactivación de turbinas en paro prolongado.
Disponibilidad. Sistema de control más confiable con tecnología nueva, redundancia en los controladores.
Confiabilidad. Operar de acuerdo con lo diseñado, mejor tecnología, mejor control.
Obsolescencia económica. Los controles mecánicos/ hidráulicos requieren márgenes de seguridad mayores que el control digital, son menos eficientes.
Mortandad del sistema de control. La vida útil promedio de los sistemas de control es de 15-20 años.
Obsolescencia técnica. Ante el desarrollo tecnológico, es posible adaptar funciones nuevas y lograr una mejor respuesta de los equipos principales.
Cambios operativos flexibles. En ocasiones, ante las exigencias del sistema eléctrico, es necesario modificar la generación de la unidad (carga base, cycling, peaking duty).
Número de unidades modernizadas |
Central | Tipo de unidad (fabricante) | Capacidad (MW) | Región de Generación de la CFE |
3 | CTG Cancún - Nizuc | TWINPACK (Pratt&Whitney) |
44 c/u | Peninsular Sur |
2 | CTG Cancún - Nizuc | W191G (Westinghouse) |
14 c/u | Peninsular Sur |
1 | CTG Cancún - Nizuc | FIAT TG20 (Fiat) |
30 | Peninsular Sur |
1 | CT MERIDA II | FIAT TG20 (Fiat) |
30 | Peninsular Sur |
1 | CT NACHICOCOM | W251B (Westinghouse) |
30 | Peninsular Sur |
1 | CTG CARMEN | (1) MW191 (Mitsubishi- Westinghouse) |
12 | Peninsular Sur |
1 | CTG XUL-HA | (1) MW191 (Mitsubishi - Westinghouse) |
14 | Peninsular Sur |
2 | CTG CHANKANAB | (1) MS-6001B |
25 12.5 |
Peninsular Sur |
2 | CTG LAGUNA-CHÁVEZ | (2) GE5001 (General Electric) |
14 c/u | Centro Norte |
14 |
CTG - Central Turbogás CT - Central Termoeléctrica
Beneficios de la modernización
Beneficios de la modernización
Las modernizaciones de sistemas de control conducen a
beneficios de grado y naturaleza variados. Las experiencias
y las mejores prácticas indican que los beneficios derivados
caen en dos categorías generales:
1. Control y Monitoreo confiable. Los beneficios técnicos que aporta son:
Desempeño: permite predecir la eficiencia de la turbina entre mantenimientos, mediante el análisis de las gráficas de tendencias históricas.
Precisión: los sistemas de control contribuyen a operar en márgenes de operación más eficientes y con mayor seguridad.
Flexibilidad: permite la personalización del sistema de control en hardware y software a requerimientos específicos de la planta.
Mayor disponibilidad en los arranques: un nuevo sistema de control puede poner a la unidad en condiciones de arranque más rápido, después de un paro.
2. Económicas. Los beneficios son notorios más en los ahorros generados que en los ingresos adicionales, y son los siguientes:
Ingresos:
Incremento en la generación: al aumentar la eficiencia y la generación, se aumenta la generación de ingresos económicos.
Ahorros:
Costos de operación: se mejora el rendimiento de la turbina, incremento en la generación, reducción de mano de obra en arranques.
Costo de partes de repuesto: no hay componentes obsoletos y las partes nuevas son accesibles y de costo competitivo.
Costo de mantenimiento: se reduce la mano de obra que daba mantenimiento al equipo obsoleto y el nuevo equipo tiene garantía y menor costo de mantenimiento.
1. Control y Monitoreo confiable. Los beneficios técnicos que aporta son:
Desempeño: permite predecir la eficiencia de la turbina entre mantenimientos, mediante el análisis de las gráficas de tendencias históricas.
Precisión: los sistemas de control contribuyen a operar en márgenes de operación más eficientes y con mayor seguridad.
Flexibilidad: permite la personalización del sistema de control en hardware y software a requerimientos específicos de la planta.
Mayor disponibilidad en los arranques: un nuevo sistema de control puede poner a la unidad en condiciones de arranque más rápido, después de un paro.
2. Económicas. Los beneficios son notorios más en los ahorros generados que en los ingresos adicionales, y son los siguientes:
Ingresos:
Incremento en la generación: al aumentar la eficiencia y la generación, se aumenta la generación de ingresos económicos.
Ahorros:
Costos de operación: se mejora el rendimiento de la turbina, incremento en la generación, reducción de mano de obra en arranques.
Costo de partes de repuesto: no hay componentes obsoletos y las partes nuevas son accesibles y de costo competitivo.
Costo de mantenimiento: se reduce la mano de obra que daba mantenimiento al equipo obsoleto y el nuevo equipo tiene garantía y menor costo de mantenimiento.
Alcance de la modernización de sistemas de control
Alcance de la modernización de sistemas de control
Las actualizaciones del sistema de control de la turbina de gas podrían cubrir cada instrumento y aspecto de control de la máquina.
Un alcance típico de una modernización del sistema de control de turbinas de gas podría incluir:
Reemplazo de instrumentos de campo como transmisores de presión, interruptores de temperatura, sensores de vibración y sensores de velocidad.
Reemplazar los interruptores por transmisores para mejorar el diagnóstico.
Reemplazo de válvulas de control de gas y combustible líquido por válvulas inteligentes modernas.
Reemplazo del controlador del gobernador.
Reemplazo de la lógica de secuenciamiento de la operación de la unidad.
Adición de Interfaz Hombre Máquina (IHM) con registro histórico de eventos/alarmas.
Reemplazo del sistema de monitoreo de vibración, que incluya sensores adicionales para mejorar el diagnóstico y evaluación de la unidad.
Los entregables básicos son:
Ingeniería básica
Ingeniería de detalle
Gabinete de control armado y alambrado
Interfaz Hombre Máquina
Control lógico, control analógico y sistema de protecciones
Puesta en servicio y operación de las unidades generadoras
Documentación (base de datos, arquitectura y comunicaciones, diagramas de control y fuerza, planos de distribución de equipo, información técnica y listas de material)
Un ejemplo de la arquitectura del sistema de control modernizado y de la Interface Hombre Máquina se muestra en las figuras 4 y 5 respectivamente.

Figura 4. Arquitectura base del sistema de control modernizado.
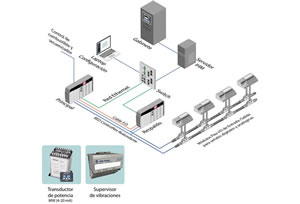
Figura 4. Arquitectura base del sistema de control modernizado.
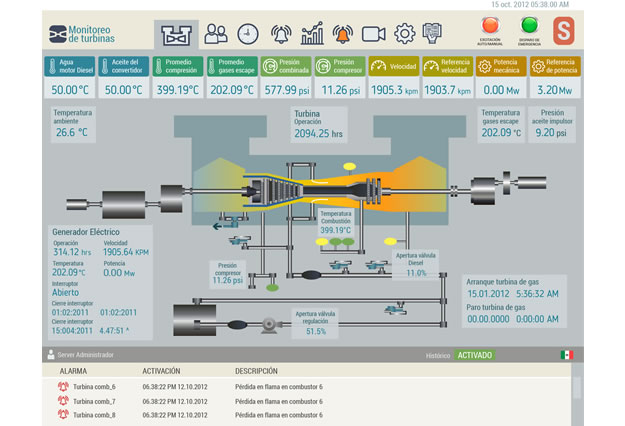
Figura 5. Pantalla principal de la Interfaz de Operación (IHM).
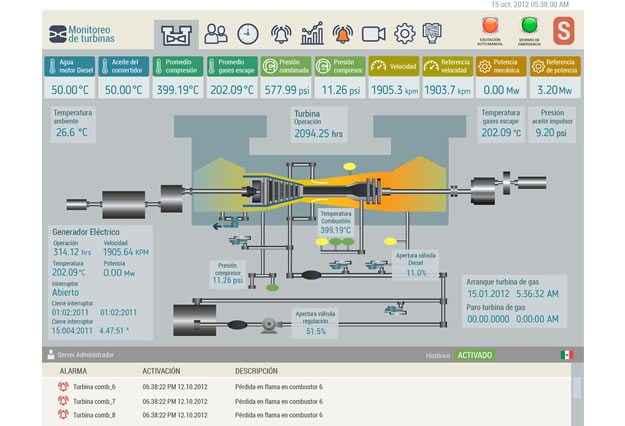
Figura 5. Pantalla principal de la Interfaz de Operación (IHM).
Recapitulación
Recapitulación
Los sistemas de control modernizados reemplazan sistemas
de control actuales para turbinas de gas, manteniendo
las filosofías de diseño y operación similares a las
originales, siendo además adaptables y configurables, e
incorporando las características que ofrecen los sistemas
de control modernos.
Gracias a la programación estructurada, usando la norma IEC 61131-3, la estrategia de control resulta sencillo de modificarse por el diseño modular del software. El uso de la norma simplifica, además, el entendimiento de las protecciones y secuencia de control por el ingeniero. Los sistemas de control modernos contienen las funciones de protección, secuenciamiento y control de combustible en procesadores modernos de alto rendimiento; la corrección y mejoramiento de los sistemas son ampliamente simplificados. Los principales beneficios son flexibilidad del control, acceso rápido a información sobre el desempeño y capacidad de diagnóstico de fallas.
Los sistemas de control moderno permiten reducir el mantenimiento de los mismos, mejorar la disponibilidad de la unidad y son mucho más fácil de operar y mantener. Soportan varios tipos de interfaces de operación, proveen capacidades adicionales de diagnóstico y manipulación de alarmas y son capaces de conectarse con otras computadoras, controladores o sistemas de control distribuido.
El Instituto Nacional de Electricidad y Energías Limpias (INEEL), siempre atento a ofrecer soluciones a la problemática del sector eléctrico, desde sus primeros años ha tenido una estrecha colaboración con la Comisión Federal de Electricidad (CFE) y a lo largo del tiempo ha diseñado, construido, instalado y puesto en servicio, sistemas de control para turbinas de gas de diversos modelos. La modernización de sus sistemas de control, le ha permitido a la CFE combatir la obsolescencia de algunas de sus centrales generadoras y, de hecho, las ha puesto nuevamente en servicio con altos niveles de seguridad, disponibilidad y confiabilidad.
Gracias a la programación estructurada, usando la norma IEC 61131-3, la estrategia de control resulta sencillo de modificarse por el diseño modular del software. El uso de la norma simplifica, además, el entendimiento de las protecciones y secuencia de control por el ingeniero. Los sistemas de control modernos contienen las funciones de protección, secuenciamiento y control de combustible en procesadores modernos de alto rendimiento; la corrección y mejoramiento de los sistemas son ampliamente simplificados. Los principales beneficios son flexibilidad del control, acceso rápido a información sobre el desempeño y capacidad de diagnóstico de fallas.
Los sistemas de control moderno permiten reducir el mantenimiento de los mismos, mejorar la disponibilidad de la unidad y son mucho más fácil de operar y mantener. Soportan varios tipos de interfaces de operación, proveen capacidades adicionales de diagnóstico y manipulación de alarmas y son capaces de conectarse con otras computadoras, controladores o sistemas de control distribuido.
El Instituto Nacional de Electricidad y Energías Limpias (INEEL), siempre atento a ofrecer soluciones a la problemática del sector eléctrico, desde sus primeros años ha tenido una estrecha colaboración con la Comisión Federal de Electricidad (CFE) y a lo largo del tiempo ha diseñado, construido, instalado y puesto en servicio, sistemas de control para turbinas de gas de diversos modelos. La modernización de sus sistemas de control, le ha permitido a la CFE combatir la obsolescencia de algunas de sus centrales generadoras y, de hecho, las ha puesto nuevamente en servicio con altos niveles de seguridad, disponibilidad y confiabilidad.
Autores:
Salvador De Lara Jayme, sdelara@ineel.mx
Luis Castelo Cuevas, lcastelo@ineel.mx
Ignacio Ramón Ramírez Palacios, irrp@ineel.mx
Miguel Angel Cristín Valdez, macv@ineel.mx
José Israel Chávez Estrada, ichavez@ineel.mx
Humberto Hernández Rosas, hhrosas@ineel.mx
Julio César Montero Cervantes, jcmc@ineel.mx
Miguel Vázquez Román, mvazquez@ineel.mx
Salvador De Lara Jayme, sdelara@ineel.mx
Luis Castelo Cuevas, lcastelo@ineel.mx
Ignacio Ramón Ramírez Palacios, irrp@ineel.mx
Miguel Angel Cristín Valdez, macv@ineel.mx
José Israel Chávez Estrada, ichavez@ineel.mx
Humberto Hernández Rosas, hhrosas@ineel.mx
Julio César Montero Cervantes, jcmc@ineel.mx
Miguel Vázquez Román, mvazquez@ineel.mx
Ciencia al descubierto
Ciencia al descubierto
Modernización de sistemas de control
para unidades generadoras del tipo turbogás
para unidades generadoras del tipo turbogás
Modernización de sistemas de control
para unidades generadoras del tipo turbogás
para unidades generadoras del tipo turbogás
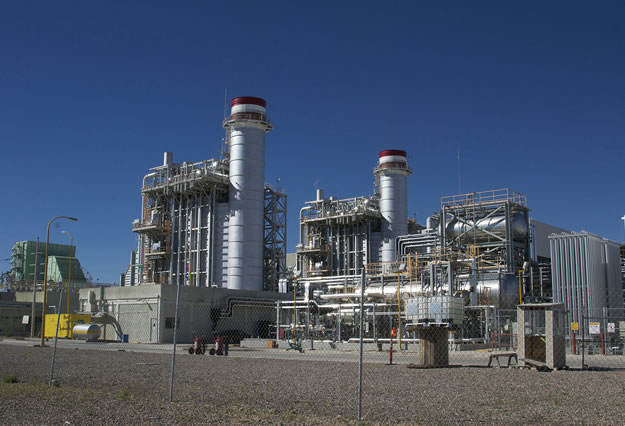
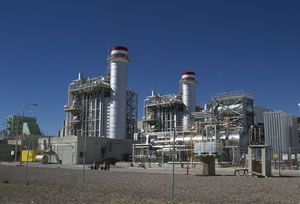
Resumen
Resumen
En este artículo se analiza la necesidad de modernizar los
sistemas de control de los equipos principales de las centrales
generadoras, con el fin de incrementar su confiabilidad
en la operación. Particularmente se describen los elementos
que justifican la modernización y cómo se relacionan con
los beneficios que podrían obtenerse. También se plantean
algunas de las justificaciones típicas que se pueden proponer
para determinar si tales modificaciones son apropiadas, así
como los alcances considerados en la modernización.
Introducción
Introducción
La generación de energía eléctrica en México actualmente
es muy diversa por su tecnología, comprende desde vapor
(combustóleo o gas), carboeléctrica, geotermoeléctrica, ciclo
combinado, turbogás, combustión interna, hidroeléctrica,
eoloeléctrica, hasta nucleoeléctrica y solar fotovoltaica. De
acuerdo con las necesidades del sistema eléctrico (demanda),
el cual suministra energía a los hogares e industrias, es el
tipo de tecnología que se utiliza para generar electricidad.
En los últimos años, más del 78% de la generación de energía eléctrica provino de tecnologías convencionales basadas en el uso de combustibles fósiles como energético primario. Estas tecnologías incluyen: carboeléctrica, ciclo combinado, combustión interna, termoeléctrica convencional y turbogás, principalmente.
De acuerdo con datos reportados por el PRODESEN 2018- 2032, el número de centrales eléctricas instaladas en México por tipo de tecnología es como lo muestra la tabla 1.
Tabla 1. Número de centrales eléctricas por tecnología. Fuente:PRODESEN 2018-2032.
En los últimos años, más del 78% de la generación de energía eléctrica provino de tecnologías convencionales basadas en el uso de combustibles fósiles como energético primario. Estas tecnologías incluyen: carboeléctrica, ciclo combinado, combustión interna, termoeléctrica convencional y turbogás, principalmente.
De acuerdo con datos reportados por el PRODESEN 2018- 2032, el número de centrales eléctricas instaladas en México por tipo de tecnología es como lo muestra la tabla 1.
Tecnología | Número de Centrales Eléctricas |
Ciclo Combinado | 83 |
Termoeléctrica Convencional | 59 |
Carboeléctrica | 3 |
Turbogás | 131 |
Combustión Interna | 248 |
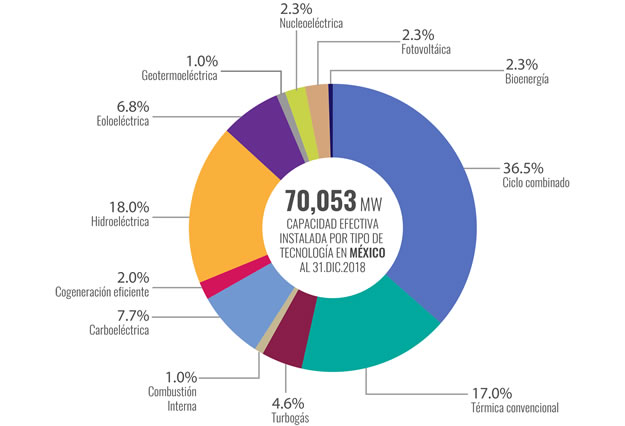
Figura 1. Capacidad efectiva instalada por tipo de tecnología, al 31 de diciembre de 2018.
Térmica convencional incluye lecho fluidizado (70,053 MW).
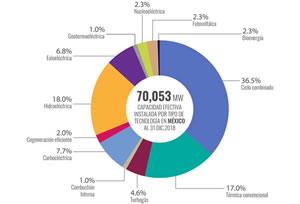
Figura 1. Capacidad efectiva instalada por tipo de tecnología, al 31 de diciembre de 2018.
Térmica convencional incluye lecho fluidizado (70,053 MW).
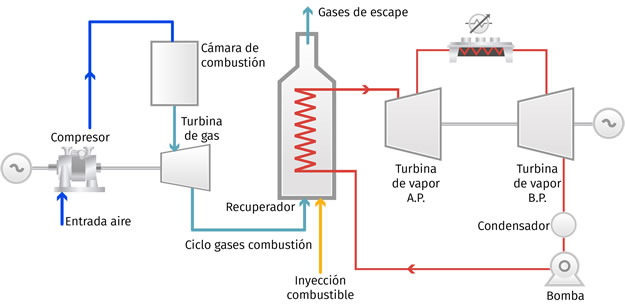
Figura 2. Diagrama simplificado de una central de ciclo combinado.
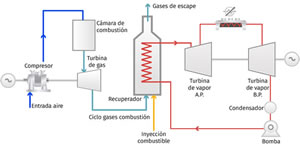
Figura 2. Diagrama simplificado de una central de ciclo combinado.
Central turbogás
Central turbogás
Una central turbogás está compuesta básicamente de un
dispositivo de arranque, un compresor, una cámara de
combustión, una turbina de gas, un generador eléctrico y
los sistemas auxiliares tales como el sistema de combustible,
el de lubricación, el de arranque, entre otros, como se
muestra en la figura 3.
El dispositivo de arranque es un equipo cuyo objetivo es asistir a la unidad de generación durante la fase de arranque, para vencer la inercia y acelerar la turbina de gas hasta la velocidad de inicio de la combustión (ignición). El compresor centrífugo presuriza el aire de la atmósfera y lo envía a la cámara de combustión, en donde se realiza la combustión del combustible gas o diésel. Los gases de escape de alta presión, producto de la combustión, se expanden en las etapas de la turbina para hacer girar a la unidad. El generador eléctrico acoplado a la turbina de gas, a velocidad nominal, es capaz de generar energía eléctrica. Finalmente, los gases de escape se descargan a la atmósfera.
Existen dos tipos principales de turbina de gas: industrial o aeroderivada; en función a su capacidad, relación de compresión, flujo de aire y temperaturas de operación, las cuales tienen respuestas y desempeños diferentes ante modificaciones de las condiciones atmosféricas.
Turbinas de gas aeroderivadas: provienen del diseño de turbinas para fines aeronáuticos, pero adaptadas a la producción de energía eléctrica en plantas industriales o microturbinas.
Turbinas de gas industriales: diseñadas para la producción de electricidad, mejorando la eficiencia para obtener una mayor cantidad de potencia y largos periodos de operación a carga máxima, disminuyendo el número de paros y arranques continuos.
Las centrales tipo turbogás tienen la ventaja de entrar en funcionamiento en poco tiempo, permitiendo abastecer rápidamente la demanda de carga eléctrica en horas de mayor demanda (hora pico). Estas pueden operar en forma de fuente de energía auxiliar o en forma permanente.
El dispositivo de arranque es un equipo cuyo objetivo es asistir a la unidad de generación durante la fase de arranque, para vencer la inercia y acelerar la turbina de gas hasta la velocidad de inicio de la combustión (ignición). El compresor centrífugo presuriza el aire de la atmósfera y lo envía a la cámara de combustión, en donde se realiza la combustión del combustible gas o diésel. Los gases de escape de alta presión, producto de la combustión, se expanden en las etapas de la turbina para hacer girar a la unidad. El generador eléctrico acoplado a la turbina de gas, a velocidad nominal, es capaz de generar energía eléctrica. Finalmente, los gases de escape se descargan a la atmósfera.
Existen dos tipos principales de turbina de gas: industrial o aeroderivada; en función a su capacidad, relación de compresión, flujo de aire y temperaturas de operación, las cuales tienen respuestas y desempeños diferentes ante modificaciones de las condiciones atmosféricas.
Turbinas de gas aeroderivadas: provienen del diseño de turbinas para fines aeronáuticos, pero adaptadas a la producción de energía eléctrica en plantas industriales o microturbinas.
Turbinas de gas industriales: diseñadas para la producción de electricidad, mejorando la eficiencia para obtener una mayor cantidad de potencia y largos periodos de operación a carga máxima, disminuyendo el número de paros y arranques continuos.
Las centrales tipo turbogás tienen la ventaja de entrar en funcionamiento en poco tiempo, permitiendo abastecer rápidamente la demanda de carga eléctrica en horas de mayor demanda (hora pico). Estas pueden operar en forma de fuente de energía auxiliar o en forma permanente.
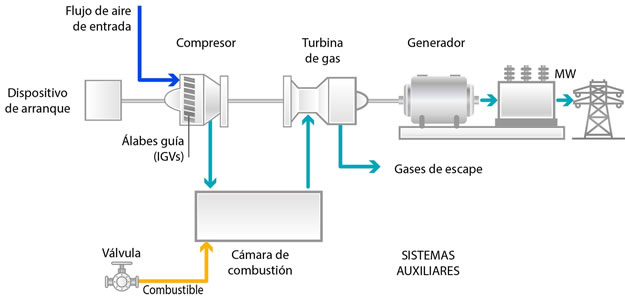
Figura 3. Diagrama simplificado de una unidad turbogás.

Figura 3. Diagrama simplificado de una unidad turbogás.
Sistema de control
Sistema de control
La unidad turbogás requiere de un sistema de control
que permita conducirla a través de las diferentes etapas
de operación, para lograr su fin que es la generación de
energía eléctrica. Estas etapas se pueden resumir de la
manera siguiente:
Arranque de la unidad desde velocidad cero hasta la velocidad de operación, que puede variar dependiendo del modelo de turbina ? generador.
Sincronización, que consiste en el proceso de conexión de la unidad turbogás a la red de distribución de energía eléctrica para aportar energía al sistema.
Generación de energía eléctrica de acuerdo con los valores establecidos por el fabricante.
Las funciones que realiza el sistema de control son básicamente las de regulación de las variables principales (velocidad, temperatura, potencia eléctrica, entre otras), supervisión y protección de la unidad generadora, incluyendo respuesta rápida, precisión y disponibilidad.
Los sistemas de control originales de las unidades turbogás de muchas centrales de la CFE se han degradado funcionalmente, ya que cuentan con más de 40 años de servicio y no existen partes de repuesto en el mercado, lo que hace que su mantenimiento sea cada vez más difícil y se presenten fallas en los arranques de las mismas. Además, existe el riesgo latente de incremento de salidas forzadas y fallas catastróficas en el equipo principal.
Si bien el equipo mecánico puede durar muchos años, el equipo de control e instrumentación tiene una vida útil limitada antes de que la obsolescencia del software o los componentes pueda dificultar cada vez más el mantenimiento, así como el del equipo instalado.
Dicha obsolescencia puede ser más importante para las empresas basadas en tecnología, donde la tecnología crítica utilizada es parte de su servicio o producción. También puede significar que ya no pueden ser competitivos dentro del mercado.
Así mismo, cabe resaltar el papel que juegan estas unidades para proporcionar energía eléctrica de emergencia en situaciones de demanda alta y/o eventos de falla de unidades de carga base, y su capacidad de arranque negro para restablecimiento expedito en el caso de un colapso del Sistema Eléctrico Nacional.
En el Instituto Nacional de Electricidad y Energías Limpias (INEEL) se han diseñado, construido, instalado y puesto en servicio, sistemas de control para turbinas de gas de diversos modelos, tal como se presenta en la tabla 2.
En estas modernizaciones se han utilizado equipos de tecnología reciente, con programación basada en estándares que permiten un mejor mantenimiento, así como ser reemplazados con mayor facilidad en un futuro, como son los Controladores Lógicos Programables (PLC, por sus siglas en inglés). Además de que es factible incluir el control digital de arranque/paro y la lógica de protecciones en el mismo equipo, con la consecuente disminución en costos.
Arranque de la unidad desde velocidad cero hasta la velocidad de operación, que puede variar dependiendo del modelo de turbina ? generador.
Sincronización, que consiste en el proceso de conexión de la unidad turbogás a la red de distribución de energía eléctrica para aportar energía al sistema.
Generación de energía eléctrica de acuerdo con los valores establecidos por el fabricante.
Las funciones que realiza el sistema de control son básicamente las de regulación de las variables principales (velocidad, temperatura, potencia eléctrica, entre otras), supervisión y protección de la unidad generadora, incluyendo respuesta rápida, precisión y disponibilidad.
Los sistemas de control originales de las unidades turbogás de muchas centrales de la CFE se han degradado funcionalmente, ya que cuentan con más de 40 años de servicio y no existen partes de repuesto en el mercado, lo que hace que su mantenimiento sea cada vez más difícil y se presenten fallas en los arranques de las mismas. Además, existe el riesgo latente de incremento de salidas forzadas y fallas catastróficas en el equipo principal.
Si bien el equipo mecánico puede durar muchos años, el equipo de control e instrumentación tiene una vida útil limitada antes de que la obsolescencia del software o los componentes pueda dificultar cada vez más el mantenimiento, así como el del equipo instalado.
Dicha obsolescencia puede ser más importante para las empresas basadas en tecnología, donde la tecnología crítica utilizada es parte de su servicio o producción. También puede significar que ya no pueden ser competitivos dentro del mercado.
Así mismo, cabe resaltar el papel que juegan estas unidades para proporcionar energía eléctrica de emergencia en situaciones de demanda alta y/o eventos de falla de unidades de carga base, y su capacidad de arranque negro para restablecimiento expedito en el caso de un colapso del Sistema Eléctrico Nacional.
En el Instituto Nacional de Electricidad y Energías Limpias (INEEL) se han diseñado, construido, instalado y puesto en servicio, sistemas de control para turbinas de gas de diversos modelos, tal como se presenta en la tabla 2.
En estas modernizaciones se han utilizado equipos de tecnología reciente, con programación basada en estándares que permiten un mejor mantenimiento, así como ser reemplazados con mayor facilidad en un futuro, como son los Controladores Lógicos Programables (PLC, por sus siglas en inglés). Además de que es factible incluir el control digital de arranque/paro y la lógica de protecciones en el mismo equipo, con la consecuente disminución en costos.
Justificación de la modernización
Justificación de la modernización
La modernización de los sistemas de control de las unidades
de generación, así como la actualización de las
Interfaces Hombre Máquina (IHM), tiene como fin principal
el mejorar la disponibilidad de las unidades y reducir los
costos de mantenimiento futuro.
Los elementos clave que justifican una modernización son:
Seguridad. Disminuir riesgo al personal, cumplir con la normatividad vigente, reactivación de turbinas en paro prolongado.
Disponibilidad. Sistema de control más confiable con tecnología nueva, redundancia en los controladores.
Confiabilidad. Operar de acuerdo con lo diseñado, mejor tecnología, mejor control.
Obsolescencia económica. Los controles mecánicos/ hidráulicos requieren márgenes de seguridad mayores que el control digital, son menos eficientes.
Mortandad del sistema de control. La vida útil promedio de los sistemas de control es de 15-20 años.
Obsolescencia técnica. Ante el desarrollo tecnológico, es posible adaptar funciones nuevas y lograr una mejor respuesta de los equipos principales.
Cambios operativos flexibles. En ocasiones, ante las exigencias del sistema eléctrico, es necesario modificar la generación de la unidad (carga base, cycling, peaking duty).
Tabla 2. Unidades Turbogás modernizadas por el INEEL.
CTG - Central Turbogás CT - Central Termoeléctrica
Los elementos clave que justifican una modernización son:
Seguridad. Disminuir riesgo al personal, cumplir con la normatividad vigente, reactivación de turbinas en paro prolongado.
Disponibilidad. Sistema de control más confiable con tecnología nueva, redundancia en los controladores.
Confiabilidad. Operar de acuerdo con lo diseñado, mejor tecnología, mejor control.
Obsolescencia económica. Los controles mecánicos/ hidráulicos requieren márgenes de seguridad mayores que el control digital, son menos eficientes.
Mortandad del sistema de control. La vida útil promedio de los sistemas de control es de 15-20 años.
Obsolescencia técnica. Ante el desarrollo tecnológico, es posible adaptar funciones nuevas y lograr una mejor respuesta de los equipos principales.
Cambios operativos flexibles. En ocasiones, ante las exigencias del sistema eléctrico, es necesario modificar la generación de la unidad (carga base, cycling, peaking duty).
Número de unidades modernizadas |
Central | Tipo de unidad (fabricante) | Capacidad (MW) | Región de Generación de la CFE |
3 | CTG Cancún - Nizuc | TWINPACK (Pratt&Whitney) |
44 c/u | Peninsular Sur |
2 | CTG Cancún - Nizuc | W191G (Westinghouse) |
14 c/u | Peninsular Sur |
1 | CTG Cancún - Nizuc | FIAT TG20 (Fiat) |
30 | Peninsular Sur |
1 | CT MERIDA II | FIAT TG20 (Fiat) |
30 | Peninsular Sur |
1 | CT NACHICOCOM | W251B (Westinghouse) |
30 | Peninsular Sur |
1 | CTG CARMEN | (1) MW191 (Mitsubishi- Westinghouse) |
12 | Peninsular Sur |
1 | CTG XUL-HA | (1) MW191 (Mitsubishi - Westinghouse) |
14 | Peninsular Sur |
2 | CTG CHANKANAB | (1) MS-6001B |
25 12.5 |
Peninsular Sur |
2 | CTG LAGUNA-CHÁVEZ | (2) GE5001 (General Electric) |
14 c/u | Centro Norte |
14 |
CTG - Central Turbogás CT - Central Termoeléctrica
Beneficios de la modernización
Beneficios de la modernización
Las modernizaciones de sistemas de control conducen a
beneficios de grado y naturaleza variados. Las experiencias
y las mejores prácticas indican que los beneficios derivados
caen en dos categorías generales:
1. Control y Monitoreo confiable. Los beneficios técnicos que aporta son:
Desempeño: permite predecir la eficiencia de la turbina entre mantenimientos, mediante el análisis de las gráficas de tendencias históricas.
Precisión: los sistemas de control contribuyen a operar en márgenes de operación más eficientes y con mayor seguridad.
Flexibilidad: permite la personalización del sistema de control en hardware y software a requerimientos específicos de la planta.
Mayor disponibilidad en los arranques: un nuevo sistema de control puede poner a la unidad en condiciones de arranque más rápido, después de un paro.
2. Económicas. Los beneficios son notorios más en los ahorros generados que en los ingresos adicionales, y son los siguientes:
Ingresos:
Incremento en la generación: al aumentar la eficiencia y la generación, se aumenta la generación de ingresos económicos.
Ahorros:
Costos de operación: se mejora el rendimiento de la turbina, incremento en la generación, reducción de mano de obra en arranques.
Costo de partes de repuesto: no hay componentes obsoletos y las partes nuevas son accesibles y de costo competitivo.
Costo de mantenimiento: se reduce la mano de obra que daba mantenimiento al equipo obsoleto y el nuevo equipo tiene garantía y menor costo de mantenimiento.
1. Control y Monitoreo confiable. Los beneficios técnicos que aporta son:
Desempeño: permite predecir la eficiencia de la turbina entre mantenimientos, mediante el análisis de las gráficas de tendencias históricas.
Precisión: los sistemas de control contribuyen a operar en márgenes de operación más eficientes y con mayor seguridad.
Flexibilidad: permite la personalización del sistema de control en hardware y software a requerimientos específicos de la planta.
Mayor disponibilidad en los arranques: un nuevo sistema de control puede poner a la unidad en condiciones de arranque más rápido, después de un paro.
2. Económicas. Los beneficios son notorios más en los ahorros generados que en los ingresos adicionales, y son los siguientes:
Ingresos:
Incremento en la generación: al aumentar la eficiencia y la generación, se aumenta la generación de ingresos económicos.
Ahorros:
Costos de operación: se mejora el rendimiento de la turbina, incremento en la generación, reducción de mano de obra en arranques.
Costo de partes de repuesto: no hay componentes obsoletos y las partes nuevas son accesibles y de costo competitivo.
Costo de mantenimiento: se reduce la mano de obra que daba mantenimiento al equipo obsoleto y el nuevo equipo tiene garantía y menor costo de mantenimiento.
Alcance de la modernización de sistemas de control
Alcance de la modernización de sistemas de control
Las actualizaciones del sistema de control de la turbina de gas podrían cubrir cada instrumento y aspecto de control de la máquina.
Un alcance típico de una modernización del sistema de control de turbinas de gas podría incluir:
Reemplazo de instrumentos de campo como transmisores de presión, interruptores de temperatura, sensores de vibración y sensores de velocidad.
Reemplazar los interruptores por transmisores para mejorar el diagnóstico.
Reemplazo de válvulas de control de gas y combustible líquido por válvulas inteligentes modernas.
Reemplazo del controlador del gobernador.
Reemplazo de la lógica de secuenciamiento de la operación de la unidad.
Adición de Interfaz Hombre Máquina (IHM) con registro histórico de eventos/alarmas.
Reemplazo del sistema de monitoreo de vibración, que incluya sensores adicionales para mejorar el diagnóstico y evaluación de la unidad.
Los entregables básicos son:
Ingeniería básica
Ingeniería de detalle
Gabinete de control armado y alambrado
Interfaz Hombre Máquina
Control lógico, control analógico y sistema de protecciones
Puesta en servicio y operación de las unidades generadoras
Documentación (base de datos, arquitectura y comunicaciones, diagramas de control y fuerza, planos de distribución de equipo, información técnica y listas de material)
Un ejemplo de la arquitectura del sistema de control modernizado y de la Interface Hombre Máquina se muestra en las figuras 4 y 5 respectivamente.

Figura 4. Arquitectura base del sistema de control modernizado.
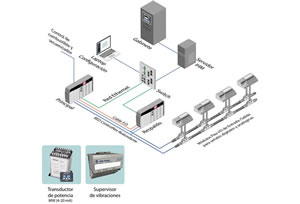
Figura 4. Arquitectura base del sistema de control modernizado.
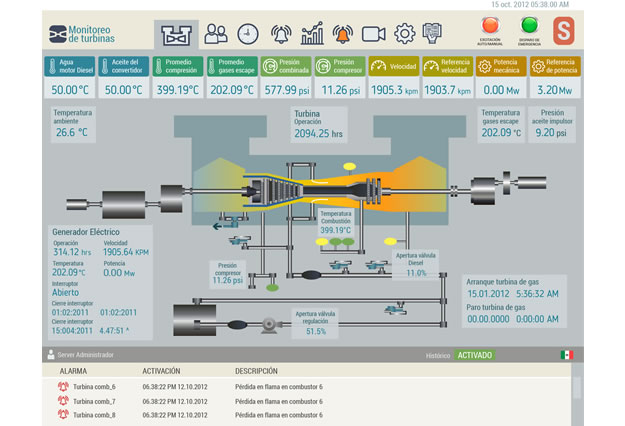
Figura 5. Pantalla principal de la Interfaz de Operación (IHM).
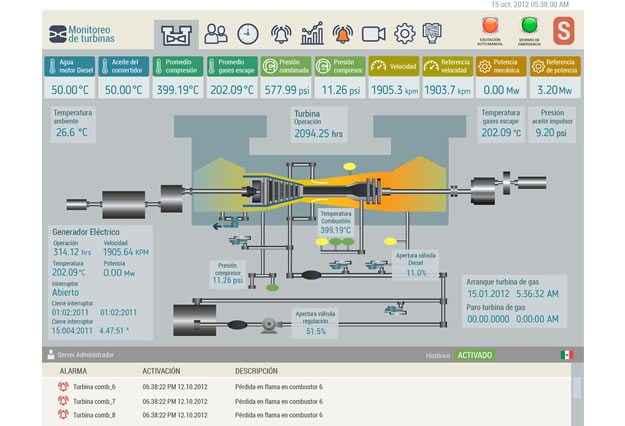
Figura 5. Pantalla principal de la Interfaz de Operación (IHM).
Recapitulación
Recapitulación
Los sistemas de control modernizados reemplazan sistemas
de control actuales para turbinas de gas, manteniendo
las filosofías de diseño y operación similares a las
originales, siendo además adaptables y configurables, e
incorporando las características que ofrecen los sistemas
de control modernos.
Gracias a la programación estructurada, usando la norma IEC 61131-3, la estrategia de control resulta sencillo de modificarse por el diseño modular del software. El uso de la norma simplifica, además, el entendimiento de las protecciones y secuencia de control por el ingeniero. Los sistemas de control modernos contienen las funciones de protección, secuenciamiento y control de combustible en procesadores modernos de alto rendimiento; la corrección y mejoramiento de los sistemas son ampliamente simplificados. Los principales beneficios son flexibilidad del control, acceso rápido a información sobre el desempeño y capacidad de diagnóstico de fallas.
Los sistemas de control moderno permiten reducir el mantenimiento de los mismos, mejorar la disponibilidad de la unidad y son mucho más fácil de operar y mantener. Soportan varios tipos de interfaces de operación, proveen capacidades adicionales de diagnóstico y manipulación de alarmas y son capaces de conectarse con otras computadoras, controladores o sistemas de control distribuido.
El Instituto Nacional de Electricidad y Energías Limpias (INEEL), siempre atento a ofrecer soluciones a la problemática del sector eléctrico, desde sus primeros años ha tenido una estrecha colaboración con la Comisión Federal de Electricidad (CFE) y a lo largo del tiempo ha diseñado, construido, instalado y puesto en servicio, sistemas de control para turbinas de gas de diversos modelos. La modernización de sus sistemas de control, le ha permitido a la CFE combatir la obsolescencia de algunas de sus centrales generadoras y, de hecho, las ha puesto nuevamente en servicio con altos niveles de seguridad, disponibilidad y confiabilidad.
Gracias a la programación estructurada, usando la norma IEC 61131-3, la estrategia de control resulta sencillo de modificarse por el diseño modular del software. El uso de la norma simplifica, además, el entendimiento de las protecciones y secuencia de control por el ingeniero. Los sistemas de control modernos contienen las funciones de protección, secuenciamiento y control de combustible en procesadores modernos de alto rendimiento; la corrección y mejoramiento de los sistemas son ampliamente simplificados. Los principales beneficios son flexibilidad del control, acceso rápido a información sobre el desempeño y capacidad de diagnóstico de fallas.
Los sistemas de control moderno permiten reducir el mantenimiento de los mismos, mejorar la disponibilidad de la unidad y son mucho más fácil de operar y mantener. Soportan varios tipos de interfaces de operación, proveen capacidades adicionales de diagnóstico y manipulación de alarmas y son capaces de conectarse con otras computadoras, controladores o sistemas de control distribuido.
El Instituto Nacional de Electricidad y Energías Limpias (INEEL), siempre atento a ofrecer soluciones a la problemática del sector eléctrico, desde sus primeros años ha tenido una estrecha colaboración con la Comisión Federal de Electricidad (CFE) y a lo largo del tiempo ha diseñado, construido, instalado y puesto en servicio, sistemas de control para turbinas de gas de diversos modelos. La modernización de sus sistemas de control, le ha permitido a la CFE combatir la obsolescencia de algunas de sus centrales generadoras y, de hecho, las ha puesto nuevamente en servicio con altos niveles de seguridad, disponibilidad y confiabilidad.
Autores:
Salvador De Lara Jayme, sdelara@ineel.mx
Luis Castelo Cuevas, lcastelo@ineel.mx
Ignacio Ramón Ramírez Palacios, irrp@ineel.mx
Miguel Angel Cristín Valdez, macv@ineel.mx
José Israel Chávez Estrada, ichavez@ineel.mx
Humberto Hernández Rosas, hhrosas@ineel.mx
Julio César Montero Cervantes, jcmc@ineel.mx
Miguel Vázquez Román, mvazquez@ineel.mx
Salvador De Lara Jayme, sdelara@ineel.mx
Luis Castelo Cuevas, lcastelo@ineel.mx
Ignacio Ramón Ramírez Palacios, irrp@ineel.mx
Miguel Angel Cristín Valdez, macv@ineel.mx
José Israel Chávez Estrada, ichavez@ineel.mx
Humberto Hernández Rosas, hhrosas@ineel.mx
Julio César Montero Cervantes, jcmc@ineel.mx
Miguel Vázquez Román, mvazquez@ineel.mx
Te podría interesar:
Te podría interesar:
Manuel Francisco Fernández Montiel