Ciencia al descubierto
Ciencia al descubierto
Tecnologías de rehabilitación y extensión
de vida útil de turbinas de vapor y gas
de vida útil de turbinas de vapor y gas
Tecnologías de rehabilitación y extensión
de vida útil de turbinas de vapor y gas
de vida útil de turbinas de vapor y gas
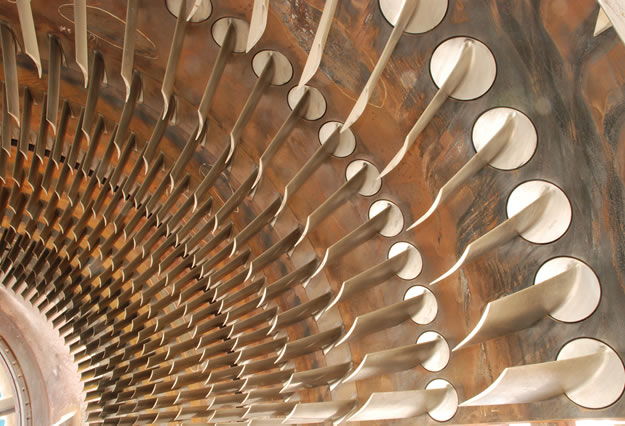
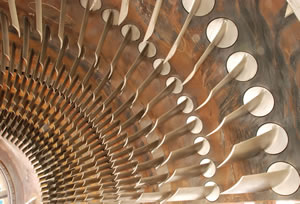
Resumen
Resumen
La disponibilidad de las turbinas de vapor y gas, así como
los costos de operación y mantenimiento, son dos de las
principales preocupaciones a nivel mundial de los operadores
de las centrales termoeléctricas. Durante el mantenimiento
programado de este tipo de turbinas se requiere el
reemplazo de componentes, especialmente en la sección
caliente, ya que estas partes sufren degradación mecánica
y microestructural por el prolongado tiempo en servicio. En
el caso de las turbinas de gas, este reemplazo representa
entre un 60 al 80% del costo total del mantenimiento. Estos
costos pueden ser reducidos en gran medida, mediante la
puesta en marcha de programas de rehabilitación y/o rejuvenecimiento
de componentes, incrementando disponibilidad,
confiabilidad y ahorros por paros forzados debidos a
fallas de componentes.
El mantenimiento y la rehabilitación de
turbinas de generación eléctrica
turbinas de generación eléctrica
El mantenimiento y la rehabilitación de
turbinas de generación eléctrica
turbinas de generación eléctrica
De acuerdo con las nuevas regulaciones del mercado eléctrico,
las turbinas de generación eléctrica operarán mucho
más de los 30 años de su vida económica (valor de diseño),
además de operar frecuentemente en regímenes de operación
flexible. Esto contribuye en un aumento en el desgaste
de sus componentes, debido a una mayor cantidad de
paros y arranques, así como de una operación a baja carga,
lo que se manifiesta en fisuras por fatiga térmica, fatiga de
altos ciclos, termofluencia, deformación, erosión, desgaste
del recubrimiento y degradación metalúrgica. Dependiendo
del tipo y grado de deterioro se pueden aplicar diferentes
métodos de rehabilitación, algunos de los cuales se presentan
a continuación:
Tecnologías y procedimientos de rehabilitación.
La rehabilitación de los diferentes componentes de las turbinas de vapor y de gas que presentan desgaste y fallas por diferentes causas, se llevan a cabo aplicando procesos específicos de soldadura:
soldadura fuerte
soldadura TIG (gas inerte de tungsteno) en cámara de gas inerte
soldadura con arco sumergido
soldadura laser
Así como de tratamientos térmicos especiales para relevado de esfuerzos o para enderezado de carcasas o flechas de rotores, aplicación de recubrimientos especiales como termo- rociado y pruebas no destructivas automatizadas para inspección de barrenos centrales de ejes de turbinas de vapor.
Para cada caso específico de componente (álabes fijos y móviles, carcasas, rotores) y tipo de falla, se requiere desarrollar la tecnología de rehabilitación, incluyendo procedimientos de inspección, caracterización de materiales con pruebas destructivas y no destructivas, ingeniería inversa y rediseño, procesos de reparación por aportes especiales de soldadura, procesos de relevado de esfuerzos, maquinado y tolerancias según el fabricante, pruebas de aceptación, montaje y puesta en servicio.
El proceso de rehabilitación se realiza normalmente en un taller especializado, o si las condiciones lo permiten en sitio, en las instalaciones de la central de generación. Después de los procesos de rehabilitación, los componentes rehabilitados deberán cumplir con las especificaciones de diseño original (dimensionales, funcionales, confiabilidad, integridad microestructural, calidad total), además, deberán presentar características superiores (mayor vida útil de 2 a 5 veces) a los componentes originales. Esto se logra con la aplicación de procesos avanzados especiales de manufactura y la modificación del diseño del componente en casos donde sea necesario.
Tecnologías y procedimientos de rehabilitación.
La rehabilitación de los diferentes componentes de las turbinas de vapor y de gas que presentan desgaste y fallas por diferentes causas, se llevan a cabo aplicando procesos específicos de soldadura:
soldadura fuerte
soldadura TIG (gas inerte de tungsteno) en cámara de gas inerte
soldadura con arco sumergido
soldadura laser
Así como de tratamientos térmicos especiales para relevado de esfuerzos o para enderezado de carcasas o flechas de rotores, aplicación de recubrimientos especiales como termo- rociado y pruebas no destructivas automatizadas para inspección de barrenos centrales de ejes de turbinas de vapor.
Para cada caso específico de componente (álabes fijos y móviles, carcasas, rotores) y tipo de falla, se requiere desarrollar la tecnología de rehabilitación, incluyendo procedimientos de inspección, caracterización de materiales con pruebas destructivas y no destructivas, ingeniería inversa y rediseño, procesos de reparación por aportes especiales de soldadura, procesos de relevado de esfuerzos, maquinado y tolerancias según el fabricante, pruebas de aceptación, montaje y puesta en servicio.
El proceso de rehabilitación se realiza normalmente en un taller especializado, o si las condiciones lo permiten en sitio, en las instalaciones de la central de generación. Después de los procesos de rehabilitación, los componentes rehabilitados deberán cumplir con las especificaciones de diseño original (dimensionales, funcionales, confiabilidad, integridad microestructural, calidad total), además, deberán presentar características superiores (mayor vida útil de 2 a 5 veces) a los componentes originales. Esto se logra con la aplicación de procesos avanzados especiales de manufactura y la modificación del diseño del componente en casos donde sea necesario.
Experiencia y aportaciones del INEEL
Experiencia y aportaciones del INEEL
Rehabilitación de álabes de turbinas de vapor
Una de las fallas más comunes es la separación de bandas remachadas y fisuras en tetones de álabes. El INEEL ha desarrollado la tecnología para rehabilitar los tetones por aporte de soldadura, con tratamientos térmico pre y post soldadura, procesos de maquinado, fabricación de nuevas bandas y control en el proceso de remachado, para garantizar tolerancias de fabricante original. En la siguiente figura se observa, del lado izquierdo, aporte por proceso TIG de pequeños cordones de soldadura y del lado derecho, tetones remachados listos para su maquinado final.
Una de las fallas más comunes es la separación de bandas remachadas y fisuras en tetones de álabes. El INEEL ha desarrollado la tecnología para rehabilitar los tetones por aporte de soldadura, con tratamientos térmico pre y post soldadura, procesos de maquinado, fabricación de nuevas bandas y control en el proceso de remachado, para garantizar tolerancias de fabricante original. En la siguiente figura se observa, del lado izquierdo, aporte por proceso TIG de pequeños cordones de soldadura y del lado derecho, tetones remachados listos para su maquinado final.
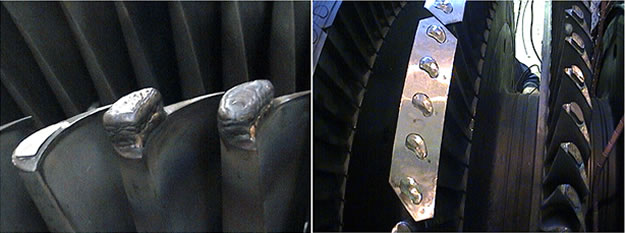
Rehabilitación de tetones de álabes por proceso TIG y proceso de remachado de los tetones.
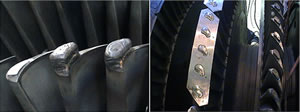
Rehabilitación de tetones de álabes por proceso TIG y proceso de remachado de los tetones.
Rehabilitación de rotores de turbinas de vapor
Las fallas en los rotores se dan principalmente en la zona de muñones con rayaduras o inclusiones, en la zona de transición entre discos y flecha se presenta erosión-corrosión, en la zona de encastre de los álabes móviles son comunes las fisuras por corrosión por esfuerzos principalmente en baja presión, las cuales son las fallas que requieren un alto grado de calidad para su rehabilitación. El INEEL ha desarrollado y supervisado procedimientos específicos, para rehabilitar daños mayores en zonas de encastre con fisuras circunferenciales, que exigen la reconstrucción completa del extremo del disco del rotor (reparaciones clase 4).
En las siguientes figuras se observan fisuras y fracturas en el disco de un rotor de baja presión, justo en la zona de encastre con los álabes móviles.
Las fallas en los rotores se dan principalmente en la zona de muñones con rayaduras o inclusiones, en la zona de transición entre discos y flecha se presenta erosión-corrosión, en la zona de encastre de los álabes móviles son comunes las fisuras por corrosión por esfuerzos principalmente en baja presión, las cuales son las fallas que requieren un alto grado de calidad para su rehabilitación. El INEEL ha desarrollado y supervisado procedimientos específicos, para rehabilitar daños mayores en zonas de encastre con fisuras circunferenciales, que exigen la reconstrucción completa del extremo del disco del rotor (reparaciones clase 4).
En las siguientes figuras se observan fisuras y fracturas en el disco de un rotor de baja presión, justo en la zona de encastre con los álabes móviles.
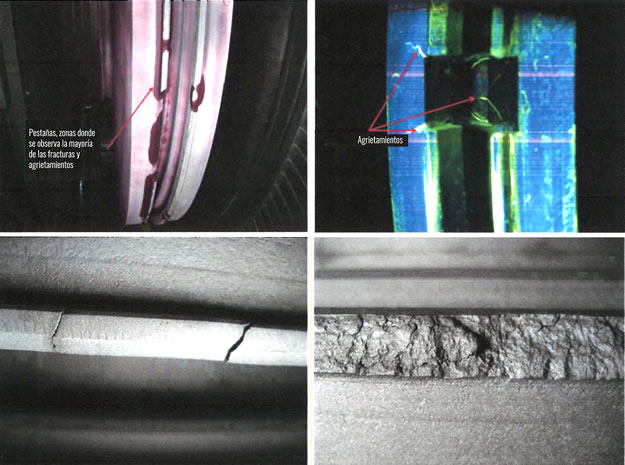
Fisuras y fracturas en el disco de un rotor de baja presión, justo en la zona de encastre con los álabes móviles.
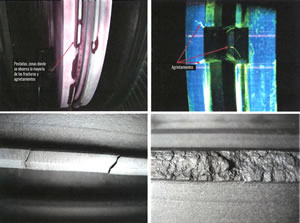
Fisuras y fracturas en el disco de un rotor de baja presión, justo en la zona de encastre con los álabes móviles.
Para la falla anterior, el INEEL desarrolló un procedimiento
específico donde la rehabilitación se realizó en un taller
especializado. Las figuras siguientes muestran el proceso
de reparación del disco del rotor. El procedimiento incluyó
caracterización de material base, apoyado en pruebas
mecánicas y metalúrgicas, selección de aporte y fundente
por proceso de arco sumergido automático, procedimiento
de soldadura por revenidos en dos pasos, inspecciones no
destructivas, tratamiento térmico post soldadura y maquinado.
Con este trabajo se recuperó el rotor de una turbina
de vapor operando de manera confiable.
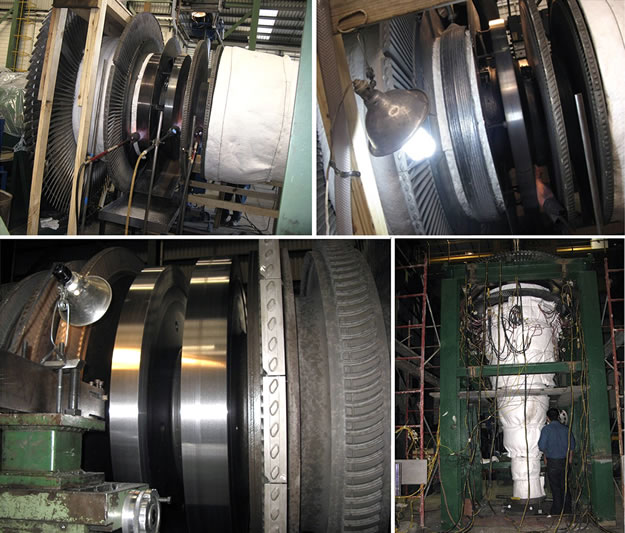
Soldadura con arco sumergido, maquinado y relevado de esfuerzos del rotor de la turbina de vapor.
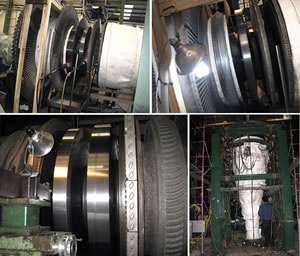
Soldadura con arco sumergido, maquinado y relevado de esfuerzos del rotor de la turbina de vapor.
Rehabilitación de válvula principal de vapor de una turbina de 158 MW
Las válvulas principales de paro de las turbinas de vapor sufren de desgaste por erosión de partículas sólidas. El INEEL desarrolló un procedimiento de rehabilitación por aporte de soldadura de revenido de dos pasos, ésta presentó características superiores a las del diseño original, ya que su vida útil se incrementó cinco veces.
En la siguiente figura se observan fallas en válvulas principales de paro (imagen superior) y en la imagen inferior se observa la simulación de los contornos de presión en una geometría de válvula, modificada por el INEEL, la cual reduce la erosión evitando la formación de fisuras.
Las válvulas principales de paro de las turbinas de vapor sufren de desgaste por erosión de partículas sólidas. El INEEL desarrolló un procedimiento de rehabilitación por aporte de soldadura de revenido de dos pasos, ésta presentó características superiores a las del diseño original, ya que su vida útil se incrementó cinco veces.
En la siguiente figura se observan fallas en válvulas principales de paro (imagen superior) y en la imagen inferior se observa la simulación de los contornos de presión en una geometría de válvula, modificada por el INEEL, la cual reduce la erosión evitando la formación de fisuras.
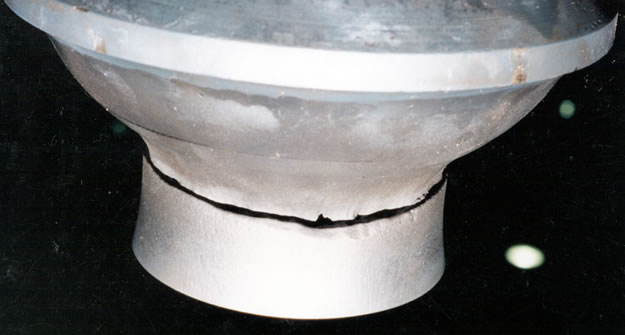
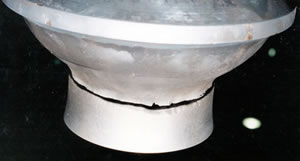
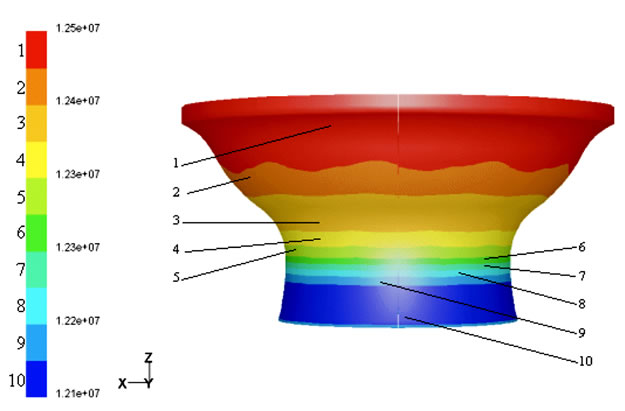
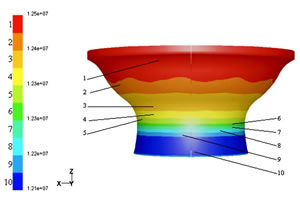
Rehabilitación de una carcasa deformada de turbina de vapor de 75 MW
La carcasa presentaba gran deformación después de un período de servicio de 40 años. Para recuperar la planicidad original de la superficie inferior y superior de la junta horizontal, el INEEL desarrolló una tecnología de rehabilitación de las carcasas en sitio, basada en el maquinado de éstas con una fresadora portátil y mandriladora, se recuperó la planicidad a los valores de diseño del fabricante.
La carcasa presentaba gran deformación después de un período de servicio de 40 años. Para recuperar la planicidad original de la superficie inferior y superior de la junta horizontal, el INEEL desarrolló una tecnología de rehabilitación de las carcasas en sitio, basada en el maquinado de éstas con una fresadora portátil y mandriladora, se recuperó la planicidad a los valores de diseño del fabricante.
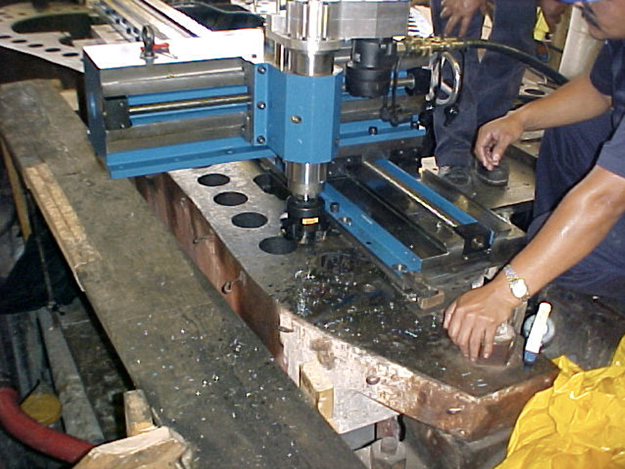
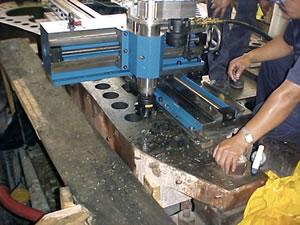
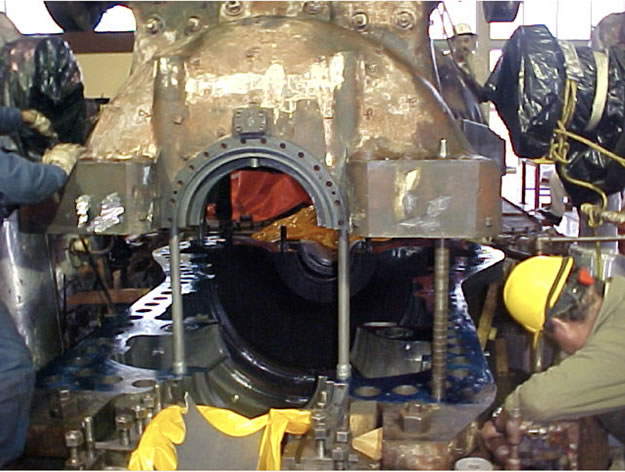
Proceso de maquinado en sitio de la carcasa y montaje de la carcasa superior ya rehabilitada.
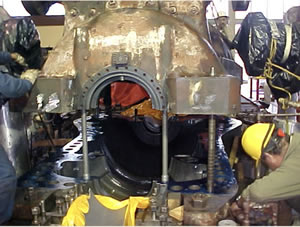
Proceso de maquinado en sitio de la carcasa y montaje de la carcasa superior ya rehabilitada.
Rehabilitación de un rotor de turbina de gas
Durante la operación comercial de una turbina de gas se presentó un incendio que resultó en daños mayores de los componentes principales de la turbina, entre ellos se dañaron las ranuras de encastre de los álabes móviles ubicadas en el disco del rotor.
El INEEL desarrolló un proceso de rehabilitación en sitio, incluyendo el procedimiento de soldadura especial de las ranuras del disco del rotor, el tratamiento térmico de relevado de esfuerzos y el maquinado de precisión de los nuevos encastres.
Durante la operación comercial de una turbina de gas se presentó un incendio que resultó en daños mayores de los componentes principales de la turbina, entre ellos se dañaron las ranuras de encastre de los álabes móviles ubicadas en el disco del rotor.
El INEEL desarrolló un proceso de rehabilitación en sitio, incluyendo el procedimiento de soldadura especial de las ranuras del disco del rotor, el tratamiento térmico de relevado de esfuerzos y el maquinado de precisión de los nuevos encastres.
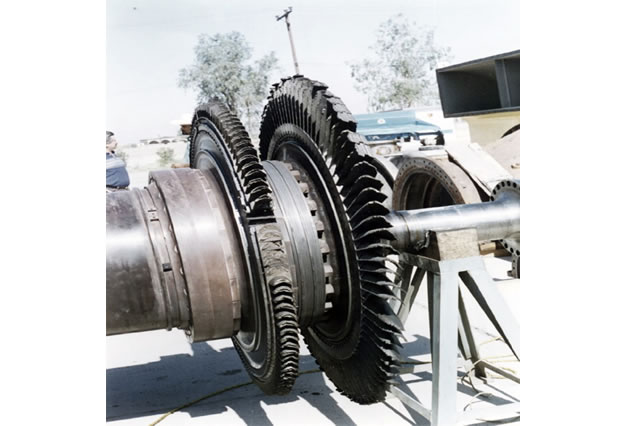
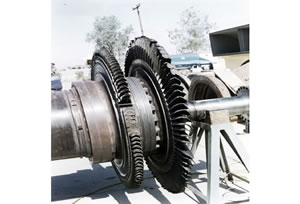
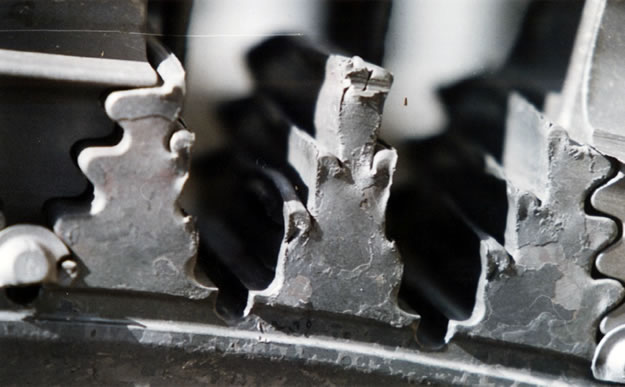
Daños en el rotor de la turbina de gas. Aspecto general (imagen superior) y detalle del daño (imagen inferior).
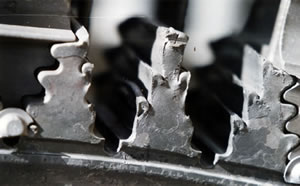
Daños en el rotor de la turbina de gas. Aspecto general (imagen superior) y detalle del daño (imagen inferior).
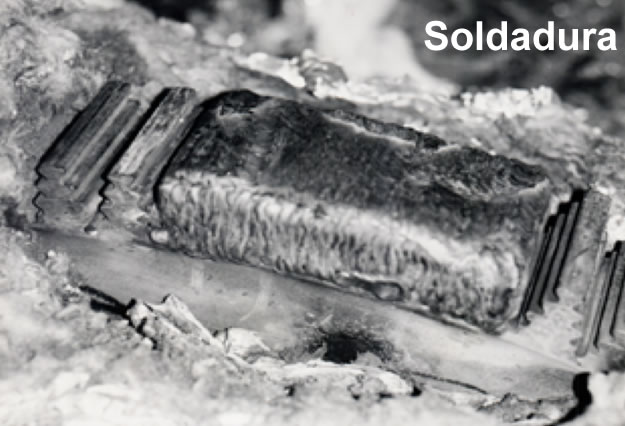
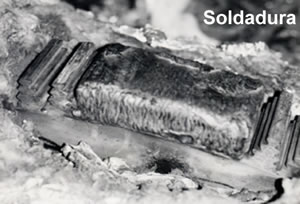
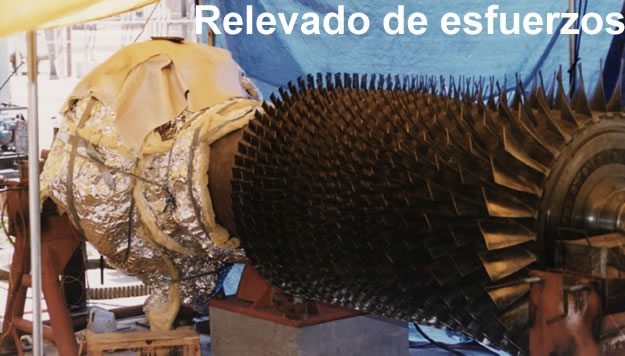
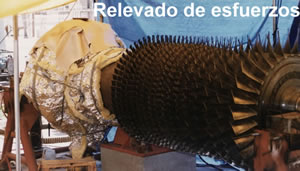
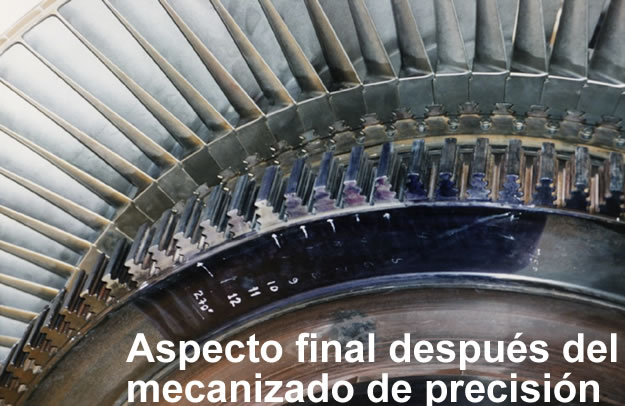
Fases de rehabilitación del rotor de turbina de gas en las instalaciones de la central de generación.
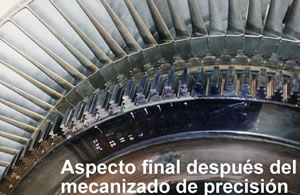
Fases de rehabilitación del rotor de turbina de gas en las instalaciones de la central de generación.
Conclusiones
Conclusiones
Debido al alto costo y tiempo de entrega de componentes
principales de turbinas de vapor y gas, el INEEL ha desarrollado
técnicas y tecnologías especiales de rehabilitación
en sitio, aplicadas con éxito en la extensión de vida útil
de carcasas, rotores, álabes móviles y fijos, y otros componentes
de las turbinas. Estas rehabilitaciones representan
un 20 o 30% del costo de las piezas nuevas, generando un
ahorro en los costos de mantenimiento de las centrales de
generación y garantizando una operación confiable en las
turbinas rehabilitadas.
Autores:
Zdzislaw Mazur Czerwiec
Alejandro Hernández Rossette, ahr@ineel.mx
Alberto Luna Ramírez, aluna@ineel.mx
Zdzislaw Mazur Czerwiec
Alejandro Hernández Rossette, ahr@ineel.mx
Alberto Luna Ramírez, aluna@ineel.mx
Ciencia al descubierto
Ciencia al descubierto
Tecnologías de rehabilitación y extensión
de vida útil de turbinas de vapor y gas
de vida útil de turbinas de vapor y gas
Tecnologías de rehabilitación y extensión
de vida útil de turbinas de vapor y gas
de vida útil de turbinas de vapor y gas
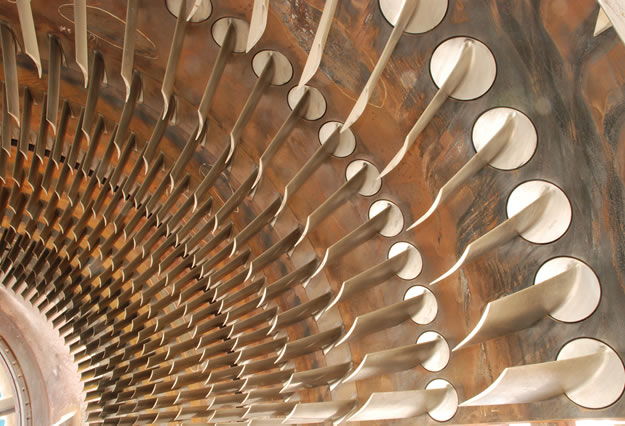
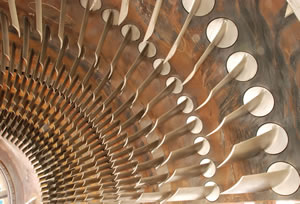
Resumen
Resumen
La disponibilidad de las turbinas de vapor y gas, así como
los costos de operación y mantenimiento, son dos de las
principales preocupaciones a nivel mundial de los operadores
de las centrales termoeléctricas. Durante el mantenimiento
programado de este tipo de turbinas se requiere el
reemplazo de componentes, especialmente en la sección
caliente, ya que estas partes sufren degradación mecánica
y microestructural por el prolongado tiempo en servicio. En
el caso de las turbinas de gas, este reemplazo representa
entre un 60 al 80% del costo total del mantenimiento. Estos
costos pueden ser reducidos en gran medida, mediante la
puesta en marcha de programas de rehabilitación y/o rejuvenecimiento
de componentes, incrementando disponibilidad,
confiabilidad y ahorros por paros forzados debidos a
fallas de componentes.
El mantenimiento y la rehabilitación de
turbinas de generación eléctrica
turbinas de generación eléctrica
El mantenimiento y la rehabilitación de
turbinas de generación eléctrica
turbinas de generación eléctrica
De acuerdo con las nuevas regulaciones del mercado eléctrico,
las turbinas de generación eléctrica operarán mucho
más de los 30 años de su vida económica (valor de diseño),
además de operar frecuentemente en regímenes de operación
flexible. Esto contribuye en un aumento en el desgaste
de sus componentes, debido a una mayor cantidad de
paros y arranques, así como de una operación a baja carga,
lo que se manifiesta en fisuras por fatiga térmica, fatiga de
altos ciclos, termofluencia, deformación, erosión, desgaste
del recubrimiento y degradación metalúrgica. Dependiendo
del tipo y grado de deterioro se pueden aplicar diferentes
métodos de rehabilitación, algunos de los cuales se presentan
a continuación:
Tecnologías y procedimientos de rehabilitación.
La rehabilitación de los diferentes componentes de las turbinas de vapor y de gas que presentan desgaste y fallas por diferentes causas, se llevan a cabo aplicando procesos específicos de soldadura:
soldadura fuerte
soldadura TIG (gas inerte de tungsteno) en cámara de gas inerte
soldadura con arco sumergido
soldadura laser
Así como de tratamientos térmicos especiales para relevado de esfuerzos o para enderezado de carcasas o flechas de rotores, aplicación de recubrimientos especiales como termo- rociado y pruebas no destructivas automatizadas para inspección de barrenos centrales de ejes de turbinas de vapor.
Para cada caso específico de componente (álabes fijos y móviles, carcasas, rotores) y tipo de falla, se requiere desarrollar la tecnología de rehabilitación, incluyendo procedimientos de inspección, caracterización de materiales con pruebas destructivas y no destructivas, ingeniería inversa y rediseño, procesos de reparación por aportes especiales de soldadura, procesos de relevado de esfuerzos, maquinado y tolerancias según el fabricante, pruebas de aceptación, montaje y puesta en servicio.
El proceso de rehabilitación se realiza normalmente en un taller especializado, o si las condiciones lo permiten en sitio, en las instalaciones de la central de generación. Después de los procesos de rehabilitación, los componentes rehabilitados deberán cumplir con las especificaciones de diseño original (dimensionales, funcionales, confiabilidad, integridad microestructural, calidad total), además, deberán presentar características superiores (mayor vida útil de 2 a 5 veces) a los componentes originales. Esto se logra con la aplicación de procesos avanzados especiales de manufactura y la modificación del diseño del componente en casos donde sea necesario.
Tecnologías y procedimientos de rehabilitación.
La rehabilitación de los diferentes componentes de las turbinas de vapor y de gas que presentan desgaste y fallas por diferentes causas, se llevan a cabo aplicando procesos específicos de soldadura:
soldadura fuerte
soldadura TIG (gas inerte de tungsteno) en cámara de gas inerte
soldadura con arco sumergido
soldadura laser
Así como de tratamientos térmicos especiales para relevado de esfuerzos o para enderezado de carcasas o flechas de rotores, aplicación de recubrimientos especiales como termo- rociado y pruebas no destructivas automatizadas para inspección de barrenos centrales de ejes de turbinas de vapor.
Para cada caso específico de componente (álabes fijos y móviles, carcasas, rotores) y tipo de falla, se requiere desarrollar la tecnología de rehabilitación, incluyendo procedimientos de inspección, caracterización de materiales con pruebas destructivas y no destructivas, ingeniería inversa y rediseño, procesos de reparación por aportes especiales de soldadura, procesos de relevado de esfuerzos, maquinado y tolerancias según el fabricante, pruebas de aceptación, montaje y puesta en servicio.
El proceso de rehabilitación se realiza normalmente en un taller especializado, o si las condiciones lo permiten en sitio, en las instalaciones de la central de generación. Después de los procesos de rehabilitación, los componentes rehabilitados deberán cumplir con las especificaciones de diseño original (dimensionales, funcionales, confiabilidad, integridad microestructural, calidad total), además, deberán presentar características superiores (mayor vida útil de 2 a 5 veces) a los componentes originales. Esto se logra con la aplicación de procesos avanzados especiales de manufactura y la modificación del diseño del componente en casos donde sea necesario.
Experiencia y aportaciones del INEEL
Experiencia y aportaciones del INEEL
Rehabilitación de álabes de turbinas de vapor
Una de las fallas más comunes es la separación de bandas remachadas y fisuras en tetones de álabes. El INEEL ha desarrollado la tecnología para rehabilitar los tetones por aporte de soldadura, con tratamientos térmico pre y post soldadura, procesos de maquinado, fabricación de nuevas bandas y control en el proceso de remachado, para garantizar tolerancias de fabricante original. En la siguiente figura se observa, del lado izquierdo, aporte por proceso TIG de pequeños cordones de soldadura y del lado derecho, tetones remachados listos para su maquinado final.
Una de las fallas más comunes es la separación de bandas remachadas y fisuras en tetones de álabes. El INEEL ha desarrollado la tecnología para rehabilitar los tetones por aporte de soldadura, con tratamientos térmico pre y post soldadura, procesos de maquinado, fabricación de nuevas bandas y control en el proceso de remachado, para garantizar tolerancias de fabricante original. En la siguiente figura se observa, del lado izquierdo, aporte por proceso TIG de pequeños cordones de soldadura y del lado derecho, tetones remachados listos para su maquinado final.
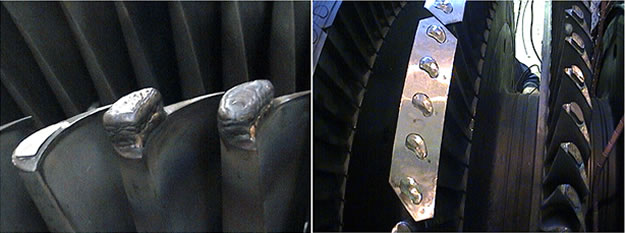
Rehabilitación de tetones de álabes por proceso TIG y proceso de remachado de los tetones.
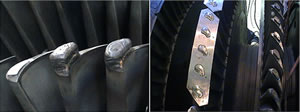
Rehabilitación de tetones de álabes por proceso TIG y proceso de remachado de los tetones.
Rehabilitación de rotores de turbinas de vapor
Las fallas en los rotores se dan principalmente en la zona de muñones con rayaduras o inclusiones, en la zona de transición entre discos y flecha se presenta erosión-corrosión, en la zona de encastre de los álabes móviles son comunes las fisuras por corrosión por esfuerzos principalmente en baja presión, las cuales son las fallas que requieren un alto grado de calidad para su rehabilitación. El INEEL ha desarrollado y supervisado procedimientos específicos, para rehabilitar daños mayores en zonas de encastre con fisuras circunferenciales, que exigen la reconstrucción completa del extremo del disco del rotor (reparaciones clase 4).
En las siguientes figuras se observan fisuras y fracturas en el disco de un rotor de baja presión, justo en la zona de encastre con los álabes móviles.
Las fallas en los rotores se dan principalmente en la zona de muñones con rayaduras o inclusiones, en la zona de transición entre discos y flecha se presenta erosión-corrosión, en la zona de encastre de los álabes móviles son comunes las fisuras por corrosión por esfuerzos principalmente en baja presión, las cuales son las fallas que requieren un alto grado de calidad para su rehabilitación. El INEEL ha desarrollado y supervisado procedimientos específicos, para rehabilitar daños mayores en zonas de encastre con fisuras circunferenciales, que exigen la reconstrucción completa del extremo del disco del rotor (reparaciones clase 4).
En las siguientes figuras se observan fisuras y fracturas en el disco de un rotor de baja presión, justo en la zona de encastre con los álabes móviles.
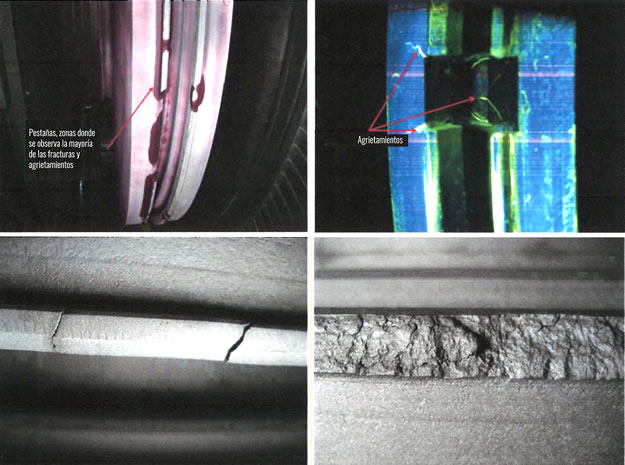
Fisuras y fracturas en el disco de un rotor de baja presión, justo en la zona de encastre con los álabes móviles.
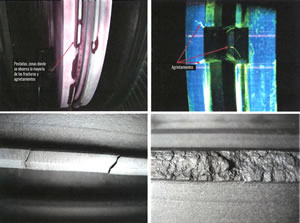
Fisuras y fracturas en el disco de un rotor de baja presión, justo en la zona de encastre con los álabes móviles.
Para la falla anterior, el INEEL desarrolló un procedimiento
específico donde la rehabilitación se realizó en un taller
especializado. Las figuras siguientes muestran el proceso
de reparación del disco del rotor. El procedimiento incluyó
caracterización de material base, apoyado en pruebas
mecánicas y metalúrgicas, selección de aporte y fundente
por proceso de arco sumergido automático, procedimiento
de soldadura por revenidos en dos pasos, inspecciones no
destructivas, tratamiento térmico post soldadura y maquinado.
Con este trabajo se recuperó el rotor de una turbina
de vapor operando de manera confiable.
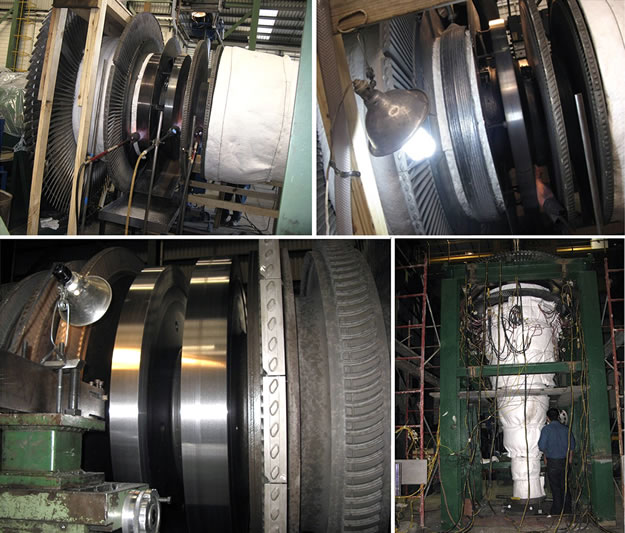
Soldadura con arco sumergido, maquinado y relevado de esfuerzos del rotor de la turbina de vapor.
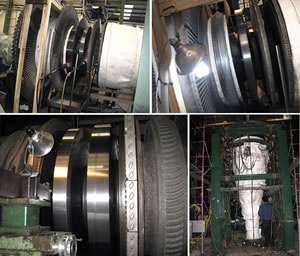
Soldadura con arco sumergido, maquinado y relevado de esfuerzos del rotor de la turbina de vapor.
Rehabilitación de válvula principal de vapor de una turbina de 158 MW
Las válvulas principales de paro de las turbinas de vapor sufren de desgaste por erosión de partículas sólidas. El INEEL desarrolló un procedimiento de rehabilitación por aporte de soldadura de revenido de dos pasos, ésta presentó características superiores a las del diseño original, ya que su vida útil se incrementó cinco veces.
En la siguiente figura se observan fallas en válvulas principales de paro (imagen superior) y en la imagen inferior se observa la simulación de los contornos de presión en una geometría de válvula, modificada por el INEEL, la cual reduce la erosión evitando la formación de fisuras.
Las válvulas principales de paro de las turbinas de vapor sufren de desgaste por erosión de partículas sólidas. El INEEL desarrolló un procedimiento de rehabilitación por aporte de soldadura de revenido de dos pasos, ésta presentó características superiores a las del diseño original, ya que su vida útil se incrementó cinco veces.
En la siguiente figura se observan fallas en válvulas principales de paro (imagen superior) y en la imagen inferior se observa la simulación de los contornos de presión en una geometría de válvula, modificada por el INEEL, la cual reduce la erosión evitando la formación de fisuras.
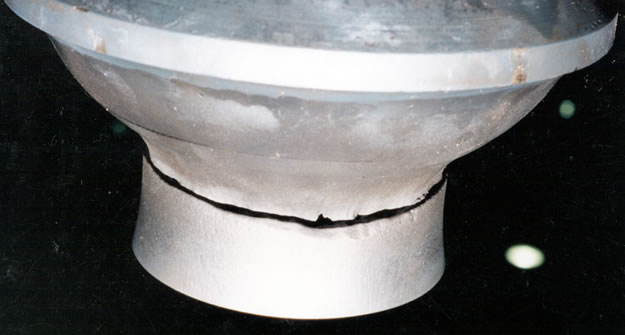
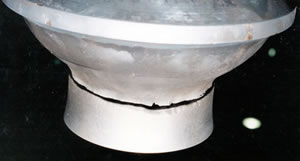
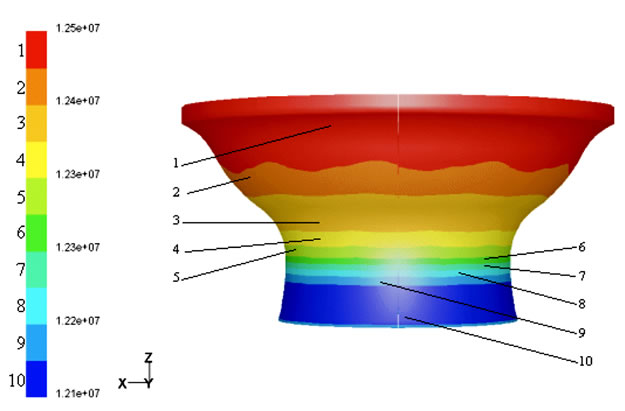
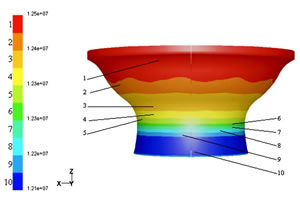
Rehabilitación de una carcasa deformada de turbina de vapor de 75 MW
La carcasa presentaba gran deformación después de un período de servicio de 40 años. Para recuperar la planicidad original de la superficie inferior y superior de la junta horizontal, el INEEL desarrolló una tecnología de rehabilitación de las carcasas en sitio, basada en el maquinado de éstas con una fresadora portátil y mandriladora, se recuperó la planicidad a los valores de diseño del fabricante.
La carcasa presentaba gran deformación después de un período de servicio de 40 años. Para recuperar la planicidad original de la superficie inferior y superior de la junta horizontal, el INEEL desarrolló una tecnología de rehabilitación de las carcasas en sitio, basada en el maquinado de éstas con una fresadora portátil y mandriladora, se recuperó la planicidad a los valores de diseño del fabricante.
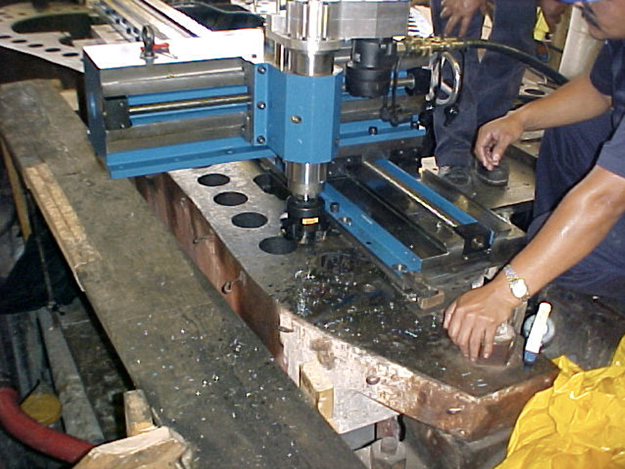
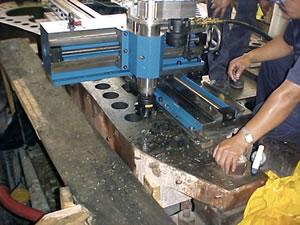
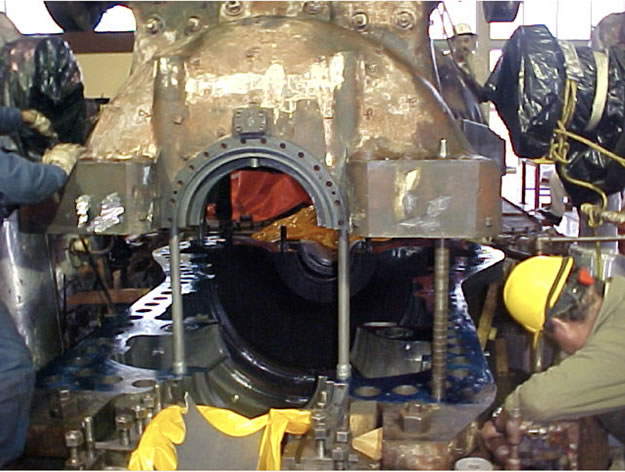
Proceso de maquinado en sitio de la carcasa y montaje de la carcasa superior ya rehabilitada.
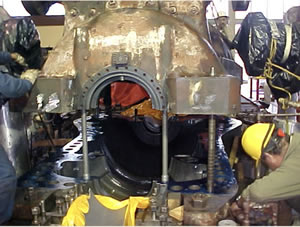
Proceso de maquinado en sitio de la carcasa y montaje de la carcasa superior ya rehabilitada.
Rehabilitación de un rotor de turbina de gas
Durante la operación comercial de una turbina de gas se presentó un incendio que resultó en daños mayores de los componentes principales de la turbina, entre ellos se dañaron las ranuras de encastre de los álabes móviles ubicadas en el disco del rotor.
El INEEL desarrolló un proceso de rehabilitación en sitio, incluyendo el procedimiento de soldadura especial de las ranuras del disco del rotor, el tratamiento térmico de relevado de esfuerzos y el maquinado de precisión de los nuevos encastres.
Durante la operación comercial de una turbina de gas se presentó un incendio que resultó en daños mayores de los componentes principales de la turbina, entre ellos se dañaron las ranuras de encastre de los álabes móviles ubicadas en el disco del rotor.
El INEEL desarrolló un proceso de rehabilitación en sitio, incluyendo el procedimiento de soldadura especial de las ranuras del disco del rotor, el tratamiento térmico de relevado de esfuerzos y el maquinado de precisión de los nuevos encastres.
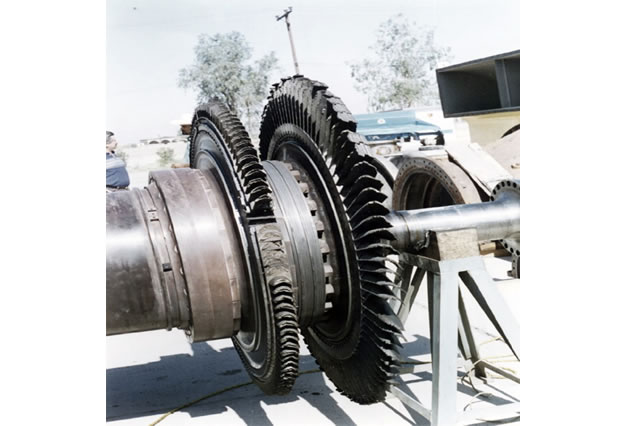
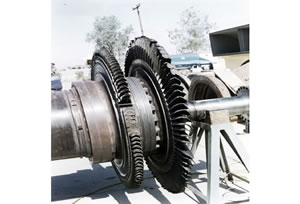
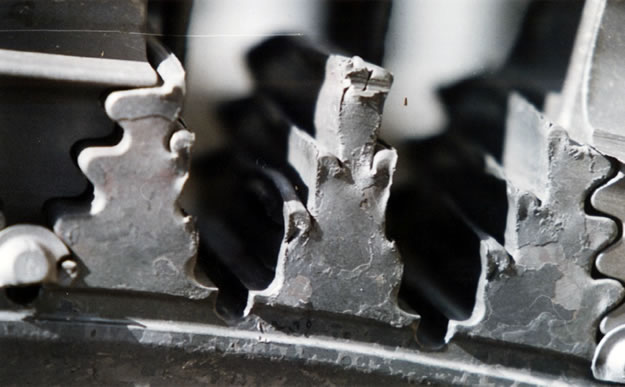
Daños en el rotor de la turbina de gas. Aspecto general (imagen superior) y detalle del daño (imagen inferior).
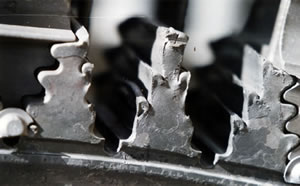
Daños en el rotor de la turbina de gas. Aspecto general (imagen superior) y detalle del daño (imagen inferior).
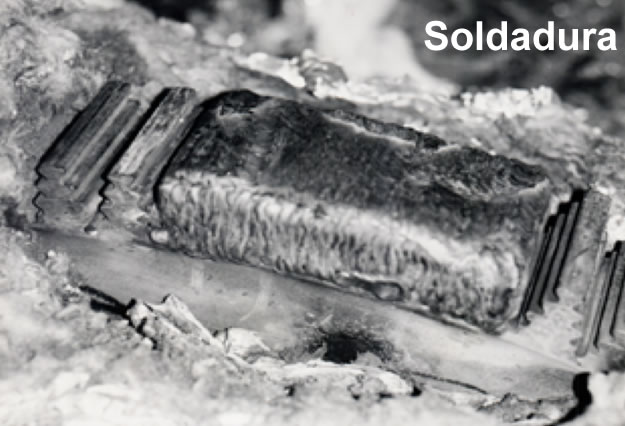
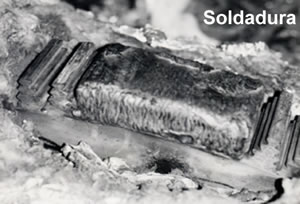
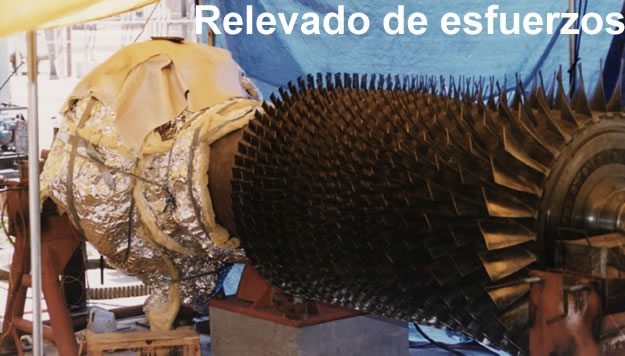
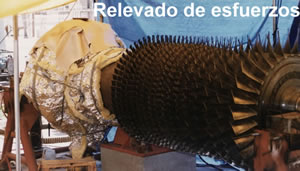
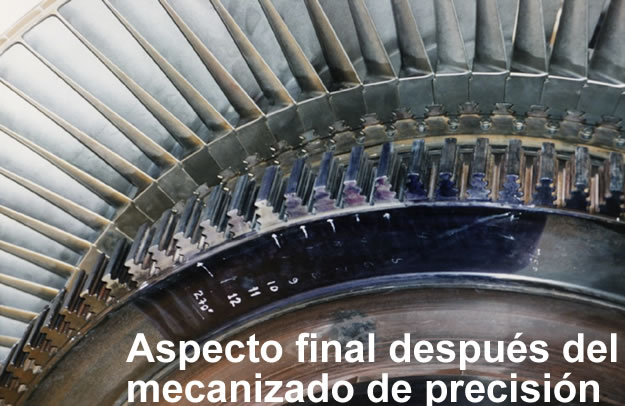
Fases de rehabilitación del rotor de turbina de gas en las instalaciones de la central de generación.
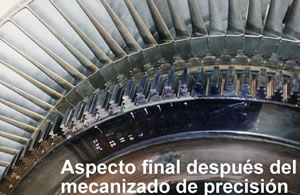
Fases de rehabilitación del rotor de turbina de gas en las instalaciones de la central de generación.
Conclusiones
Conclusiones
Debido al alto costo y tiempo de entrega de componentes
principales de turbinas de vapor y gas, el INEEL ha desarrollado
técnicas y tecnologías especiales de rehabilitación
en sitio, aplicadas con éxito en la extensión de vida útil
de carcasas, rotores, álabes móviles y fijos, y otros componentes
de las turbinas. Estas rehabilitaciones representan
un 20 o 30% del costo de las piezas nuevas, generando un
ahorro en los costos de mantenimiento de las centrales de
generación y garantizando una operación confiable en las
turbinas rehabilitadas.
Autores:
Zdzislaw Mazur Czerwiec
Alejandro Hernández Rossette, ahr@ineel.mx
Alberto Luna Ramírez, aluna@ineel.mx
Zdzislaw Mazur Czerwiec
Alejandro Hernández Rossette, ahr@ineel.mx
Alberto Luna Ramírez, aluna@ineel.mx
Te podría interesar:
Te podría interesar:
Isaías Ramírez Vázquez, Ramiro Hernández Corona, Alberto Hernández Valdez, Alberto Brito Luisillo, Julio César Vergara Vázquez, David Ponce Noyola, Fernando Ramírez Malpica y Manuel Ávila Rodríguez