Ciencia al descubierto
Confiabilidad operacional en procesos industriales, un enfoque modular y progresivo
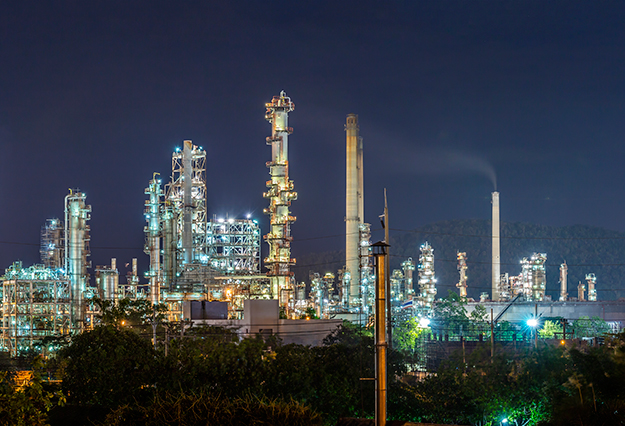
Introducción
Existen factores externos e internos que influyen sobre el
desempeño económico de las instalaciones industriales. Si
bien los factores externos son determinados por fuerzas
ajenas a las organizaciones, tales como las condiciones de
la economía y el mercado, el entorno político, entre otros,
sobre los factores internos se pueden tomar acciones
proactivas que mejoran el desempeño económico de los
procesos industriales.
Uno de los aspectos internos que influye de manera importante
sobre el desempeño de un proceso productivo es la
disponibilidad (i.e. la probabilidad de que un proceso esté
operable en un instante dado). Por ejemplo, los paros no
programados, causa de indisponibilidad, producen pérdidas
por suspensión de la producción; y en los incidentes o
accidentes, además de las pérdidas de producción, influyen
negativamente en el ánimo de los equipos de trabajo.
La disponibilidad de los procesos está fuertemente influida
por la confiabilidad de los equipos (i.e. la probabilidad
de que un equipo opere durante un intervalo de tiempo
determinado), las acciones humanas y la calidad de la
base documental que rige la relación entre ellos. Dicha
base documental incluye procedimientos e instrucciones
de operación y mantenimiento, bases de diseño, manuales,
entre otros documentos, y contribuye favorable o desfavorablemente
a la confiabilidad de equipos y de recursos
humanos. Lograr el buen desempeño de los tres elementos:
equipos, humanos y la base documental que los relaciona,
es fundamental para mejorar y controlar el desempeño
económico de los procesos.
A lo largo del tiempo se han desarrollado diversas herramientas
metodológicas que, cuando se aplican de forma
adecuada, son de gran utilidad para mejorar, controlar y
supervisar aspectos específicos de la confiabilidad de los
procesos. Por ejemplo, en lo que respecta a la confiabilidad
de los equipos, una metodología que ha demostrado
generar ahorros y mejoras es el Mantenimiento Centrado en Confiabilidad (RCM, por sus siglas en inglés).
El RCM
se
ha aplicado con éxito en diversas industrias como la aeronáutica,
la petrolera, la automotriz, la militar, entre otras.
Al igual que el RCM, existen otras metodologías que están
orientadas a mejorar aspectos específicos de los procesos,
así como propuestas con un enfoque más integral, un
ejemplo de ello es la confiabilidad operacional, integrada
por cuatro áreas: la confiabilidad de equipo, la confiabilidad
humana, la confiabilidad del proceso y la confiabilidad
del diseño, tal como se muestra en la Figura 1.
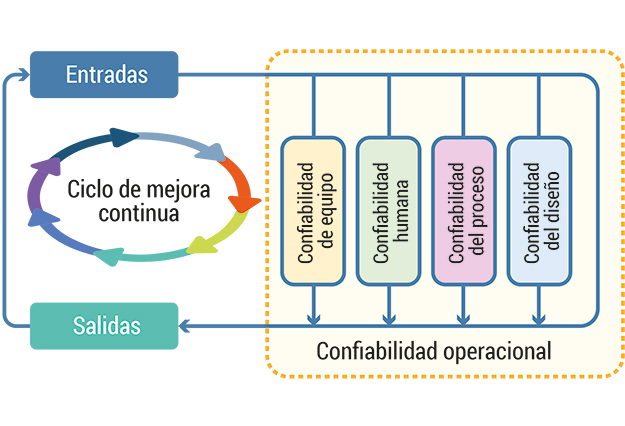
Figura 1. Áreas de la confiabilidad operacional.
El concepto de confiabilidad operacional aparece en las
últimas tres décadas. Algunos autores explican la confiabilidad
operacional como "la capacidad de una instalación
o sistema para cumplir su función, dentro de los límites de
diseño y bajo un contexto operacional específico"1.
Por una parte, existen metodologías especializadas en
aspectos específicos de la confiabilidad, por otra, existen
propuestas con una visión más integral y tenerla reporta
más beneficios que la aplicación aislada de las metodologías
especializadas o específicas, sin embargo, se debe
tener precaución en la forma en que se establece esa integración,
ya que por un lado puede dar origen a un método
complejo de implementación, y por otro, pudiera requerir
grandes esfuerzos antes de que se observen los beneficios.
Lo anterior podría provocar el rechazo por parte de
posibles usuarios o propietarios de procesos industriales
debido al nivel de esfuerzo e inversión necesaria, así como
al periodo requerido para que una herramienta de este
tipo pueda aportar resultados.
Por lo anteriormente expuesto, es valioso contar con una
propuesta integral que aproveche tanto los beneficios de
las metodologías específicas, como las sinergias que originan
las interacciones y complementariedad de esas metodologías, tal como se esquematiza en la Figura 1,
asegurando que su implantación sea práctica mediante
un esquema modular y progresivo. Hecho de esa manera,
los grupos responsables de la toma de decisiones pueden
aspirar a realizar esfuerzos alcanzables con presupuesto
razonables, y atestiguar los beneficios en tiempos más
cortos. Así mismo, los grupos de trabajo pueden ir adaptándose
a los nuevos paradigmas, creando así una cultura
de mejora de la confiabilidad.
La confiabilidad operacional en un ciclo de mejora continua
Si se parte de las cuatro áreas de la confiabilidad operacional como centro de un sistema de mejora de la confiabilidad de un proceso industrial, se requiere proveer de complementos que de manera sistemática le den funcionalidad. Esos complementos se muestran en la Figura 2.
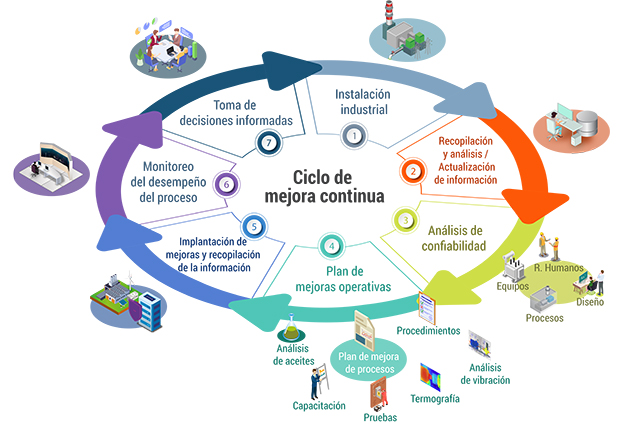
Figura 2. Ciclo de mejora continua de la confiabilidad operacional.
El ciclo inicia con la selección de un proceso industrial (1), del cual se debe recopilar la información (2) que permita aplicar los métodos de la confiabilidad de equipos, de la confiabilidad humana, de la confiabilidad del proceso y de la confiabilidad del diseño (3), cada una de ellas permitirá identificar mejoras operativas, lo que puede dar origen a un plan de mejoras operativas del proceso (4). Cuando se implantan esas mejoras y se continúa con la operación y el registro de información (5), a través de mecanismos como el monitoreo de desempeño del proceso (6) se puede determinar la efectividad de los cambios y generar información que puede apoyar los procesos de toma de decisiones (7). El esquema planteado permite mantener el nivel de desempeño deseado de un proceso productivo y con ello se establece un ciclo natural de mejora continua.
Enfoque modular del ciclo de mejora continua de la confiabilidad operacional
El esquema presentado en la Figura 2 integra los elementos necesarios para dar funcionalidad, en un ciclo de mejora continua, a las áreas de confiabilidad operacional mostradas en la Figura 1. Ese esquema organiza los elementos de forma lógica, aprovechando las ventajas que provee la aplicación de metodologías independientes, especializadas en mejorar áreas específicas de la confiabilidad, no obstante, se debe tener cuidado en la forma de implantación de la Figura 2, ya que puede dar origen a un proceso de implantación complejo y demandante de recursos. Para evitar esta situación, se diseñó un esquema de implantación modular y progresivo (Figura 3), que plantea la integración de metodologías independientes y especializadas que mejoran las diferentes áreas de la confiabilidad. La implantación también plantea el uso de una herramienta informática para facilitar su aplicación y seguimiento, así como para identificar de manera oportuna las desviaciones sobre el desempeño deseado. Una de las ventajas de esta propuesta radica en el hecho de que cada elemento modular identifica oportunidades de mejora de la confiabilidad operacional que, una vez implantadas, se reflejarán en los indicadores de desempeño del proceso en periodos cortos.
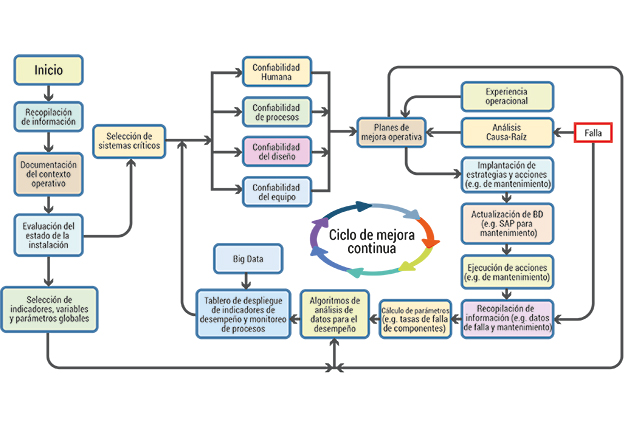
Figura 3. Esquema de implantación modular y progresivo de la confiabilidad operacional del INEEL.
El esquema de implantación comienza con la
recopilación
de información
de la instalación. Al realizarse de forma sistemática,
esa actividad permite determinar el estado de la
base documental que soporta la operación y el mantenimiento
de la instalación. Entre las acciones que se pueden
realizar, se analiza si la información está completa, actualizada,
legible, disponible, concentrada y controlada. Además,
se encuentran: la especificación del diseño, manuales, procedimientos,
políticas, descripción de perfiles y responsabilidades,
entre otras. El beneficio de realizar esta actividad
reside en identificar oportunidades de mejora respecto al
estado de la base documental que norma la relación entre
personas y equipos.
Después de la recopilación de la información está el
módulo
de documentación del contexto operativo
, en el cual se
describe cada modo de operación (i.e. la forma o estado en
el que funciona el proceso), se identifican capacidades del
proceso, subprocesos, sistemas y componentes, así como los rangos normales de operación, las metas de
producción
y los tiempos para alcanzarlas, su relación con los insumos,
entre otros detalles.
En algunos procesos industriales, la desactualización de la
documentación sobre capacidades de sistemas, equipos
o componentes, o la falta de definición de los rangos de
operación aceptables han conducido a accidentes e incidentes.
Además, es común que con el tiempo se hagan
modificaciones al proceso, que pueden involucrar cambios
en suministros, filosofía de operación o mantenimiento, e
incluso al diseño, entre otros, y que no se han reflejado de
manera formal en las memorias técnicas de documentación
del proceso, por lo que documentar el contexto operativo
es fundamental para establecer la única referencia
válida para evaluar y dar seguimiento al desempeño del
proceso o equipos.
Con el análisis de la información y el establecimiento
del contexto operativo se está en posibilidad de
evaluar
el estado de la instalación
o del proceso, y la evaluación
puede hacerse con respecto al mismo proceso, considerando
que todo funciona de manera ideal. Esta evaluación
podría apuntar a las oportunidades de mejora más
evidentes del proceso y que podrán corroborarse con los
análisis posteriores.
Después del módulo de evaluación del estado de la instalación,
una salida conduce al
módulo de selección de
indicadores, variables y parámetros globales de desempeño
,
el cual, de manera sistemática, permite determinar
el conjunto de información a monitorear, relacionada con
el desempeño global del proceso industrial y que apoya la
toma de decisiones. La otra salida conduce al
módulo de
selección de sistemas críticos
. Para procesos industriales
complejos e integrados por muchos sistemas es necesario
contar con criterios y/o métodos, para seleccionar los
sistemas más importantes. La aplicación de ese módulo
provee el orden de importancia de los sistemas y se puede
usar como guía para la asignación de recursos para mantenimiento.
También se usa para determinar los sistemas
a los cuales se les aplicarán los métodos especializados
que soportan la aplicación de las áreas de la confiabilidad
operacional:
confiabilidad humana, confiabilidad
de equipo, confiabilidad de procesos y confiabilidad del
diseño
. Cada método que soporta las áreas de la confiabilidad
operacional permite identificar acciones de mejora
en su especialidad.
Las acciones de mejora de la confiabilidad operacional
se concentran en el módulo de planes de mejora operativa,
donde se priorizan las mejoras, y se da seguimiento
al estado de los programas de implantación, estado de las
acciones, fechas de inicio, conclusión y responsables. Una
de las salidas de ese módulo envía información sobre el
estado de implantación de las mejoras al
módulo de algoritmos
de análisis de datos para el desempeño
, el cual
soportará su despliegue en el tablero de monitoreo. La otra salida se dirige hacia el módulo de
implantación de
estrategias
y acciones (e.g. de mantenimiento).
En el
módulo de implantación de estrategias y acciones
(e.g. de mantenimiento)
, el usuario contará con el soporte
para gestionarlas, incluyendo la
actualización de la base
documental
y la ejecución de las estrategias (e.g. el mantenimiento).
Una vez que las estrategias y acciones se
implanten, y ejecuten, se comienza a disponer de datos
(e.g. datos de falla y de mantenimiento). Con esos datos
se alimenta el módulo de recopilación de información y
se pueden encontrar oportunidades de ahorro y mejora.
Ese módulo le permite al usuario disponer de un registro
histórico y sistemático de datos para alimentar al
módulo
de cálculo de parámetros
; por ejemplo, parámetros como
la tasa de falla de componentes. Siendo la tasa de falla, el
número de fallas por unidad de tiempo. Con el resultado
de este último módulo se pueden alimentar algoritmos de
análisis para determinar valores como la confiabilidad de
sistemas, la disponibilidad de procesos y apoyar la toma
de decisiones.
El
módulo de algoritmos de análisis de datos para el
desempeño
permite adquirir datos desde diversas partes
del proceso, los concentra, realiza los análisis requeridos y
los integra para generar información con valor. Por ejemplo,
los rangos de operación correcta y los valores en los cuales
se deben emitir alertas de desviaciones que pueden llegar
a convertirse en daños a equipos, pérdida de producción, o
altos consumos de insumos, entre otras. Con base en esta
información se pueden tomar decisiones de manera directa,
o si fuera requerido, se pueden integrar a algoritmos predictivos
de la ocurrencia de fallas, u otros cálculos, que
permitan soportar el proceso de toma de decisiones.
Finalmente, el
tablero de despliegue de indicadores de
desempeño y monitoreo de procesos
muestra de manera
selectiva e integrada la información del proceso en forma
gráfica e histórica. Esa información es la más relevante para
la confiabilidad operacional del proceso productivo, incluye los indicadores clave de desempeño, así
como las
variables
y parámetros de operación global del proceso y los específicos
de los equipos. Así mismo, es aquí donde se generan
las alertas de las desviaciones en etapas incipientes para
una oportuna intervención. El monitoreo de toda la información
generada en el proceso servirá para retroalimentar
al mismo sistema. Posteriormente se pueden realizar
correcciones sobre alguna o las cuatro áreas de la confiabilidad,
manteniendo el proceso en un ciclo virtuoso de
mejora continua.
Como módulos complementarios y opcionales se pueden
considerar: un módulo para realizar análisis causa-raíz de
eventos relevantes; un módulo para dar seguimiento a la
experiencia operacional interna y externa; un módulo para
análisis big data, y otras herramientas analíticas predictivas.

Experiencia del INEEL y beneficios
El INEEL cuenta con amplia experiencia en la aplicación
de varias técnicas y métodos que conforman la confiabilidad
operacional y que se han aplicado en el desarrollo de
diversos proyectos para el sector energético, tanto para las
áreas eléctrica como petrolera, y en la industria automotriz.
Para el caso particular de la confiabilidad de equipos,
se han desarrollado proyectos en instalaciones petroleras
marítimas de bombeo de petróleo crudo, compresión,
deshidratación y endulzamiento de gas amargo. Debido al
grado de detalle capturado en el proceso de documentación,
la mayoría de las instalaciones adoptaron esa documentación,
no sólo para modificar los planes y programas
de mantenimiento, sino como material bibliográfico para entrenamiento de nuevos operadores y personal
técnico en
general.
En procesos de generación eléctrica se tiene amplia experiencia
en Análisis de Riesgos y Análisis de Confiabilidad
para centrales de generación hidroeléctrica, dentro de las
que se incluyeron sistemas como la obra de toma, la turbina
hidráulica, el generador eléctrico, el sistema de excitación,
el sistema de enfriamiento del generador y el sistema
de distribución de corriente directa que se utiliza tanto en
los sistemas de regulación automática de voltaje, como en
el sistema de protecciones eléctricas, entre otros.
En procesos de transmisión de energía eléctrica se han
analizado transformadores de potencia, autotransformadores,
reactores e interruptores de potencia.
Incluso se han aplicado esas mismas técnicas y métodos a
la industria automotriz, cuyos procesos tienen características
distintas a los sectores eléctrico y energético.
Algunos de los beneficios obtenidos al hacer la implantación
y dar seguimiento a las técnicas de confiabilidad operacional
incluyen:
- El incremento de la disponibilidad y productividad mediante la reducción de paros no programados.
- La optimización y sistematización de la generación y actualización de planes de mantenimiento, con enfoque en la reducción de costos.
- Valores de referencia para la atención oportuna de la desviación del desempeño deseado de los procesos, cuando se encuentran en su etapa incipiente.
- Preservación de los aspectos fundamentales de la experiencia del personal sobre la operación y el mantenimiento de equipos y sistemas, como medida ante la rotación o jubilación del personal.
Conclusiones
Implantar las cuatro áreas de la Confiabilidad Operacional
(CO) de manera simultánea puede dar origen a un problema
complejo y demandante de recursos, razón por la
cual se diseñó un esquema de implantación de la CO que
es modular y progresivo. Adicionalmente, el esquema incorpora
complementos que le dan funcionalidad, de manera
sistemática, en un ciclo de mejora continua.
El esquema planteado simplifica un proceso complejo y
provee, a quienes tengan interés en implantarlo, los elementos
para hacerlo de forma gradual sin perder la visión
integral, permitiéndoles ajustar el alcance. Lo anterior
podría incluir desde la revisión sistemática de la base
documental de los procesos, hasta el uso de técnicas analíticas
avanzadas para soportar la toma de decisiones, con
enfoque a la excelencia operativa de la industria.
El esquema modular lo hace accesible a procesos industriales
grandes, medianos y pequeños. Cada módulo, de
forma independiente, tiene el potencial para identificar
oportunidades de mejora de la CO en los procesos industriales
y los resultados pueden reflejarse en el corto plazo.
1 Referencia: Parra, C., Crespo, A., Fygueroa, S., "Modelo integral para optimizar la confiabilidad en instalaciones petroleras", 2° Congreso Mundial de Mantenimiento y 19° Congreso Brasileño de Mantenimiento, Brasil, 2004.
Autores:
Roberto Calixto Rodríguez, rcalixto@ineel.mx
Salvador Sandoval Valenzuela, sandoval@ineel.mx
Rogelio Rea Soto, rrea@ineel.mx